BI V2.0 – A self-replicating, high precision 3D Printer
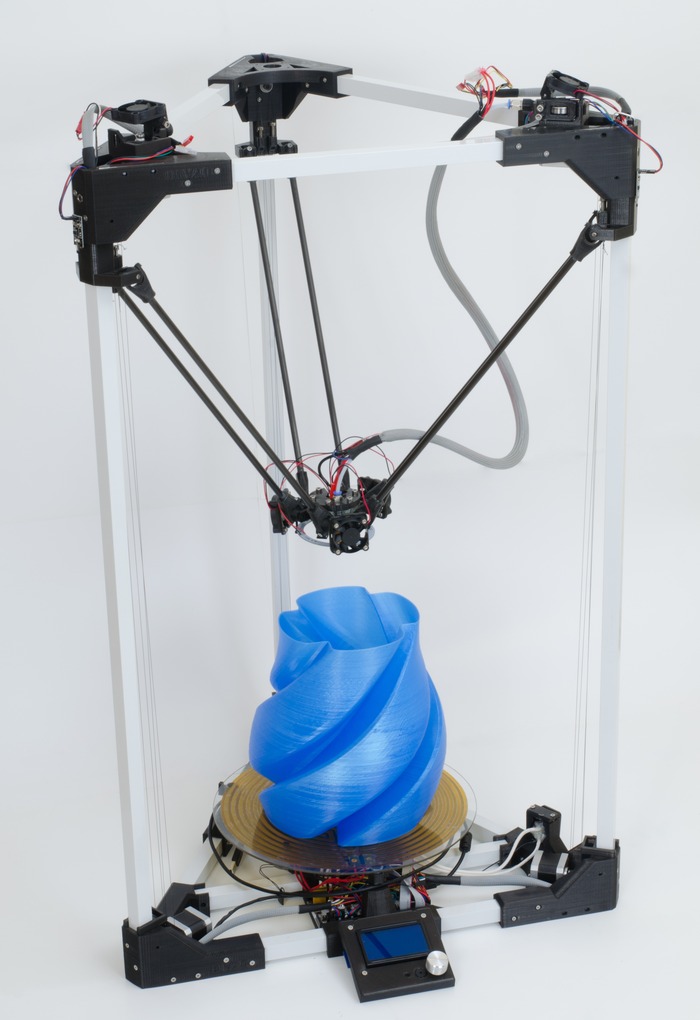

The Boots Industries BI V2.0 is a delta style 3D printer featuring widely available and self-replicating 3D printed components. Innovation is at the forefront of the reinforced frame and triple pulley system, allowing for a large build volume and high quality 3D printed pieces.

Kickstarter printers will be the first to ship before we open the BI V2.0 on our online store. Act now and be the first to get your hands on it!
What is 3D printing?
3D printing is an exciting technology that allows the everyday user to create 3 dimensional objects from various plastics. Nearly any object you can imagine is built layer by layer by continuously pushing plastic through a ”hot end” with a narrow tip that positions the molten plastic on the build surface of your BI V2.0.
Why BI V2.0?
The BI V2.0 capably produces very large 300 mm diameter X 300 mm height prints and features an amazing print quality (Be sure to read more about the definition of a true delta build volume below). Our design can support up to triple extrusion and can print virtually any 1.75 mm filament extruding at up to 240 degrees Celsius (PLA/ABS/Nylon etc.). The most unique aspect of the BI V2.0 is our innovative approach towards a self-replicating design which permits the simple creation of extremely precise movement. The end result: the highest standards of print quality. The self-replicating design of the BI V2.0 empowers you to create your own machine and share this technology with your family and friends. Once you receive the BI V2.0, you can print, improve upon and share components so that anyone can build their own printer at a very low cost.
Our assembled components remove the longest and trickiest steps from the equation (i.e. stringing the pulleys, wiring the towers etc.). With our simple to follow instructions the partial assembly will take between 30 minutes and an hour of work.

How did the BI V2.0 come about?
Boots Industries was founded in 2012 by Jean Le Bouthillier, MSc and François Crête, BEng with a goal of making 3D printing more accessible by offering high quality at an affordable price. After the successful concept development and creation of the BI V1.0 (As well as the sale of many kits and fully assembled versions), a significant amount of positive feedback, suggestions and feature requests were received. The BI V2.0 represents the evolution of our work considering these facts on delta style printers and reinforces our core belief that with the right components and a little bit of ingenuity there are no limits in terms of the creation of a high precision, large build volume 3D printer at a relatively low cost.
Thanks to several key design features, the BI V2.0 is capable of producing high quality prints in either PLA, ABS, Nylon or a variety of materials extruding at up to 240 degrees Celsius.


The entire structure of the BI V2.0 is made of steel reinforced 3D printed corners and 3/4 inch anodized aluminium extrusions. The vertical aluminum extrusions serve a dual purpose, acting as structural and linear motion components. Within the context of a delta robot, the most important precision factor is the vertical displacement of each tower. The combination of vertical displacements moves the delta platform around the build volume. This particularity of delta robots allows us to use 3D printed linear bearings without sacrificing any precision. 3D printed linear bearings are also more silent than their ball bearing counterparts. The final result is a clean, practical and dual purpose design.


To ensure maximum precision during vertical displacement of the delta towers we use high powered NEMA 17 motors with 32x Microstepping (This delights the user with the highest possible resolution). We also use a non-stretch, 50 lb test spectra line which, unlike traditional drive belts, will never stretch during accelerations prompted by your print requests. Finally, we use a triple pulley system which automatically keeps the delta arms of each tower level. The result is a high precision motion accomplished with low cost and widely available components.


This project also features a redesigned 0.4 mm JHead for the extruder hot end (This will be called the Jhead BI Edition). This hot end comes with a modified 4 mm push fitting that allows the PTFE tube to lock in place. Our modifications allow you to print at higher speeds and clogging is virtually non-existent, because our design doesn’t allow backflow. The filament is only capable of moving in one direction – out the nozzle towards the creation of everything you can imagine!
The BI V2.0 can be controlled without a computer through the use of a conveniently positioned LCD controller. With its large LCD screen, this controller provides the user with a unique and remarkable computer free experience. All the key functionalities are found on the LCD. The user has the ability to move the printer, set speeds, temperatures and start prints when their G Code is stored on the SD Card. The Bi V2.0 comes standard with the LCD controller and a 4 GB SD card which can contain an average of 2500 print files.

It should be obvious that warp prevention and proper adhesion of your parts to the build surface are truly critical features. For this reason, all BI V2.0 3D printers will ship out with a heat bed as a standard feature as opposed to a cost option. Our heat bed comprises a heat foil, glass and a magnetic fastening system. In addition, the bed features a triple point adjustment mechanism to make macro adjustments.

Our delta platform is built with carbon fibre rods, 3D printed PLA, a laser cut acrylic tooling insert and is ready for multiple extrusions with a capacity of up to three hot ends. At present, we continue to fine tune the settings and procedures (Retraction settings, hot end vertical alignment) to accomplish high quality dual extrusion. We have previously accomplished this on several experimental models and are confident that delivery of this feature under quality control is more than within our capabilities. We will continue work in this area and we plan to publish an update video featuring double extrusion in the future. A second extruder kit is available as an upgrade option for any pledge level above including a BI V2.0 Kit.

The purpose of an auto-level probe is to measure the height of your print bed at various points and automatically adjust the height of the print nozzle depending on current location. We feel that this is another critical feature since the probe not only measures the height of the print bed, but also resolves discrepancies in the system as a whole. The result is a consistent layering across the entire 300 mm diameter. Printing at such a large diameter without the assistance of the auto-level probe would be very tricky and frustrating – near impossible. As such our printers come standard with the auto-level probe!

Our goal is empowerment of the user to create their own printers and improve our design with their ideas. For this reason, all of our 3D models will be made open source in the Sketchup format. We chose the Sketchup format because you won’t need to unnecessarily dedicate resources towards CAD software that isn’t readily accessible or affordable.
Concerning the build volume of a Delta printer
In the context of delta printers there is an important distinction that must be made between the volume contained inside the towers, defined by the print bed, and the actual size of objects the printer is capable of producing. Indeed, in order to offer a true 300 mm diameter X 300 mm height build volume certain clearances must be designed into the printer. Due to the geometry of delta printers and the size of the delta platform it is not possible to print directly to the edge of the circular print bed without leaving a clearance equal or greater than the delta platform dimension between the tower and the heat bed. This means that when a delta design features a circular print bed with no clearance from the towers there will always exist an unreachable zone on the outermost perimeter. Likewise, a vertical clearance must be left above the delta carriages when printing at the maximum height. Without this clearance, the carriages would hit the top structural corners and would never be able to reach the full diameter when printing at the maximum height. An important feature of our design pertaining to the geometry is that our build area is contained within the equilateral triangle created by the three towers. This is due, in large part, to the fact that the team found that this configuration offered the highest precision during the prototyping phase.

Additional features of the BI V2.0 include:
- Sleeved electrical wiring for a clean look.
- Quick disconnect wires in the most convenient places to facilitate maintenance and reconfiguration.
- Triple fan assembly to maintain consistent temperatures.
- Powerful LED ring to see the printer in action.
What’s in the BI V2.0 kit?
Our kit will ship partially assembled with the following components:
- Fully assembled X, Y and Z towers pre-wired with NEMA 17, cable drive system and carriages
- Fully assembled delta platform with arms, fans, hot end and auto-level probe
- Extruder electrical/PTFE tubing “umbilical” cord
- Pre-cut and pre-drilled aluminium extrusions
- Rumba board with DRV 8825 drivers
- 12V/29A Power supply
- Hardware bag (nuts, bolts, spare parts etc.)
- LCD control panel assembly





Thank you Notes
We would like to thank Mr. Johann Rocholl for his work on the Rostock 3D printer.
We would like to thank the Marlin firmware contributors.
We would like to thank the Repetier Host team for their excellent software.
We would like to thank all of customers and the Rostock BI V1.0 adopters for their input.
3D models for all parts (source files) will be released once our Kickstarter Campaign comes to an end! The company currently plans to start and regularly contribute to an online Wiki to further knowledge and research into this promising design.
Risks and challengesLearn about accountability on Kickstarter
We’ve spent a lot of time preparing the BI V2.0 for production and we also have experience designing and producing our anterior version the BI V1.0.
Careful Delivery Schedule:
We’ve created an initial Kickstarter delivery schedule that is reasonable, leaves room for adaptation and won’t exceed our current production capability. If demand increases we will look at ways to manufacture a greater number of units and add additional pledges.
Acquiring the components:
We are already printing all the 3D printed components and have the ability to scale our production (by using more printers) to meet any demand. We are already one of the top Canadian supplier of PLA and ABS filament and also offer other electrical components for 3D printing. We have secured new contracts with our electronics manufacturers to produce the electronics in bulk. We also have a new supplier for the 3/4 inch aluminium extrusions.
Final modifications:
Although our BI V2.0 is definitely ready for production, we still plan to make several last minute “cosmetic” improvements. For example we will be tweaking the lengths of electrical wires and sleeving around the delta head. These modifications will not impact the delivery schedule of the BI V2.0, but we felt it was important to mention that we will tweak a few details to make your printers look even better!
Assembling the kits for delivery:
Our kits will be shipped partially assembled and we want to ensure that the kits are built in a consistent and accurate way between runs. Our goal and challenge will be to train employees to complete the pre-assembly perfectly every time. Having spent a lot of time with prototypes and anterior versions we designed a final assembly which is very simple to put together.
Shipment packaging:
Although the BI V2.0 components are quite rigid and won’t break easily, we want to explore ways to package the kit in a way that result in the lowest footprint and the highest safety during shipping. We will be working with local providers specialized in product packaging.
Your satisfaction:
We want to make sure that you receive all the required information on how to assemble, calibrate and use the software to it’s full potential. We feel that we will accomplish this by providing online videos, articles, a wiki and dedicated support on all aspect of the BI V2.0. Although we won’t rely on it; we also think that a community of users will develop around the V2.0 and that users will be able to help each other and share tips and tricks.