NAIAS 2018: Schaeffler Showcases Environmentally Friendly Drive Systems
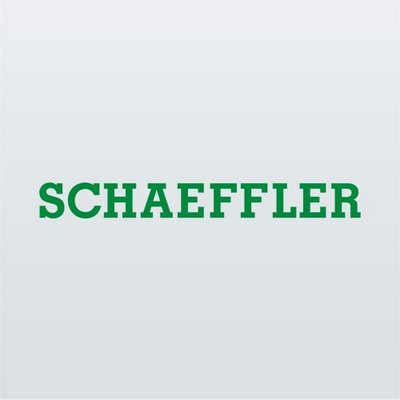
DETROIT, Jan. 16, 2018 /PRNewswire/ — Electric mobility will continually increase over the next few years. By 2030, as much as 30 percent of all newly produced cars could be using all-electric traction systems, according to a recently proposed scenario. In that case, 40 percent would have a hybrid powertrain and only 30 percent would exclusively be equipped with an internal combustion engine (ICE).
To equip its global customers with production-ready solutions for the evolving automotive marketplace, Schaeffler is showcasing its portfolio of low-emission and locally zero-emissions driving for all three engine systems at the 2018 North American International Auto Show (NAIAS).
Electrification Solutions
Considerable potential improvement is offered by the electrification of conventional powertrains and Schaeffler’s 48-volt system is a relatively low-cost solution. In current production vehicles, this system, instead of a starter-generator, is connected to the crankshaft of the internal combustion engine via a belt.
At the 2018 NAIAS, Schaeffler will present its solution for future vehicle generations: the integration of the 48-volt electric motor into the engine-transmission unit and into the axle. Provided that an electric motor with the requisite power output and a battery with sufficient capacity are used, solutions like this even make “active coasting” possible at higher speeds – the vehicle maintaining its speed in spite of the ICE being shut off. In addition to enabling considerable reductions in fuel consumption, the energy generated in deceleration phases can be recovered more effectively. For example, the electric power gained as a result may be used to operate an electrically heatable catalytic converter and to thus achieve emission levels far below current legal requirements.
Hybrid Developments
A plug-in hybrid powertrain enables even greater fuel consumption savings to be achieved as well as driving with local zero emissions across longer distances. For more than 10 years, Schaeffler has been working on the central element of such a powertrain, the high-voltage hybrid module. Production of the next-generation hybrid module is about to be launched and will enable the transfer of very high torques of up to 800 Nm. A patented branching of the power flow within the module makes it possible to transfer such high torques. In addition, the hybrid module can be combined with the converter in automatic transmissions so that even vehicles with very large mass – such as car-trailer combinations commonly used in the North American market – can comfortably accelerate from a complete stop.
Particularly suitable for battery-electric vehicles are traction systems that are integrated into the axle or even into the wheels. While the electric wheel hub motor is still a predevelopment topic, volume production of the electric axle from Schaeffler is imminent. Currently, the supplier’s engineers are working on four electric axle production projects in parallel.
IC Engine Solutions
Even in the most extreme scenarios, two in three new vehicles would still have an ICE on board, so Schaeffler offers solutions to further reduce the emissions of internal combustion engines.
At NAIAS, Schaeffler is presenting its second-generation thermal management module that is now making its debut in volume production in the United States in 2018. This module controls the cooling circuits of the engine, the transmission and additional electric drive units, if applicable, plus that of the battery. At the beginning of the warm-up phase, all cooling circuits can be completely shut off to enable accelerated heating of the individual systems. The circuits managed by the module can be systematically controlled, depending on operating conditions and heat requirements in the vehicle’s cabin.
The actuators used in the thermal management module influence the functionality and service life of the engine as well. Schaeffler has developed a modular kit that is tailored to the respective automaker’s requirements. The use of a thermal management module makes it possible to achieve up to three percent improved fuel economy and even more following a cold start at low outdoor temperatures.
The dynamic timing of the engine’s valves is another important influencing variable. The reason is that a major portion of the total engine emissions is produced in acceleration phases. Engine designers can effectively counter this by short-term adjustment of the opening and closing times of the intake valves through which air and recirculated exhaust gas flow into the cylinder. To enable fast adjustment even in dynamic driving modes, Schaeffler has developed an electric camshaft adjuster and successfully introduced it into volume production with a major global automaker.
“Using electromechanical technology, it is now possible to adjust the camshaft at a crankshaft angular velocity of 600 to 800 degrees per second,” said Prof. Peter Gutzmer, CTO, Schaeffler. “And this adjustment is even possible in the opposite direction of the engine’s rotation, which is notable since the hydraulic systems that have been widely used so far are slower by a factor of two to 10, depending on engine speed and temperature.”
Greater variability, less consumption and lower emissions: these advantages are provided as well by systems that shut off one or more cylinders in low-load driving conditions. As a result, the cylinders that remain active operate in a more efficient load range. The hydraulic-switchable valve tappet developed by Schaeffler allows individual cylinders to be deactivated. In 2018, the first three-cylinder engine using such a system from Schaeffler will go into production. A dual-mass flywheel with an integrated pendulum-type absorber – another product developed by Schaeffler – prevents negative effects by the temporary two-cylinder operation on the engine’s NVH (acoustics, vibration and harshness) performance.
“At the moment, no one can tell how soon fully electric vehicles will become widely accepted in the marketplace,” says Gutzmer. “It is clear, though, that the entire automotive industry is on the road toward zero-emissions mobility. We intend to support this trend with technologies that are ready for production.”
About Schaeffler
The Schaeffler Group is a global automotive and industrial supplier. Top quality, outstanding technology, and exceptionally innovative spirit form the basis for the continued success of the company. By delivering high-precision components and systems in engine, transmission, and chassis applications, as well as rolling and plain bearing solutions for a large number of industrial applications, the Schaeffler Group is already shaping “Mobility for tomorrow” to a significant degree. The technology company generated sales of approximately EUR 13.3 billion in 2016. With around 89,400 employees, Schaeffler is one of the world’s largest family companies and, with approximately 170 locations in over 50 countries, has a worldwide network of manufacturing locations, research and development facilities, and sales companies.
Schaeffler is a recognized development partner for global automakers and suppliers. To serve the North American automotive market, Schaeffler operates development centers in: Troy, Mich.; Fort Mill, S.C.; Wooster, Ohio; and Puebla, Mexico. The company’s 600 North American engineers and technicians, who are supported by a team of more than 6,700 global R&D engineers, drive development in the region by utilizing state-of-the-art test and measurement equipment, computational tools and CAD systems. Schaeffler Automotive has headquarters in Fort Mill and manufacturing facilities in: South Carolina; Missouri; Ohio; Ontario, Canada; Puebla and Irapuato, Mexico. For more information, please visit www.schaeffler.us.
Follow us on Twitter @schaefflergroup to get all of our latest press releases and news.