How Hydraulics Are Used in Aerospace
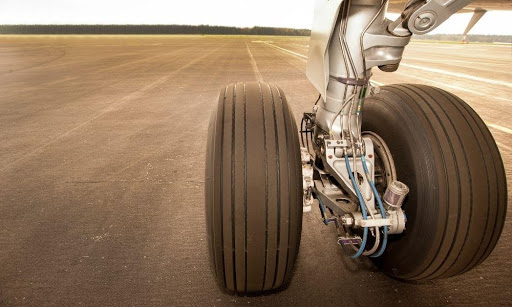
Once upon a time, man looked up at the sky and thought, “Why not?” Since then, humans have found countless ways to achieve their vision, whether through kites large enough to carry a person, clockwork dragons, dirigibles, or balloons. Nowadays, taking to the skies is no longer unusual, and that’s partially thanks to the wonder of hydraulics. They may not be the plane’s wings or engines, but how hydraulics are used in aerospace is certainly noteworthy.
Brakes
If you know anything about cars, then the idea of hydraulics being used for brakes won’t be unusual for you. Similar principles can be applied to how hydraulics are used in aerospace braking. A master cylinder feeds hydraulic fluid through a brake line. The pressure from the brakes distributes through the fluid to the disc and brake pads. The disc and brake pads clamp onto the wheels, and the friction stops the plane. The hydraulic system may also be affected by a hydraulic charge pump that may replenish lost fluid.
This works well for a smaller aircraft, but what about a commercial airliner? These systems utilize the same hydraulic technology to activate the brake system. However, in order to generate enough heat energy to stop a plane of that size, the system uses a series of alternating brake pads and discs rather than two on either side of the wheel. Along with this, many larger aircraft like Boeing airliners have an autobrake system that employs the hydraulic brakes through software technology.
Landing Gear
The average airplane weighs 175,000 lbs. when it lands, including the weight of the plane itself, as well as the fuel, passengers, and cargo. On average, they land at 150-165 mph. You don’t have to be an expert in physics to know that this will add up to disaster without additional help. That’s where hydraulics come to save the day yet again by powering a plane’s landing gear, specifically its shock absorbers.
The type of shock absorber used on modern large aircraft combines hydraulics and pneumatics, or a system that utilizes pressurized gas. The oleo-pneumatic shock absorber is located in dual cylinders just above a plane’s wheels. The upper cylinder contains a gas such as nitrogen, while the lower cylinder contains hydraulic fluid. When the plane lands, the fluid of the lower cylinder compresses the air of the upper cylinder. The upper cylinder then takes the full shock of the landing.
Shuttle Engines
Hydraulics don’t just work in our atmosphere. Hydraulics’ uses in aerospace also extends to space shuttles. Along with helping power a shuttle’s brakes and landing gear, they also provide thrust vector control to the engines. Thrust vectoring refers to an engine’s ability to control the direction of thrust. Without it, shuttles won’t take off in the correct direction. Traditionally, this has been done with a hydraulic or electrohydraulic actuator. This actuator gimbals the engines in the correct direction to ensure that the shuttles take off vertically.