Different Types of Sheet Metal Used in Fabrication
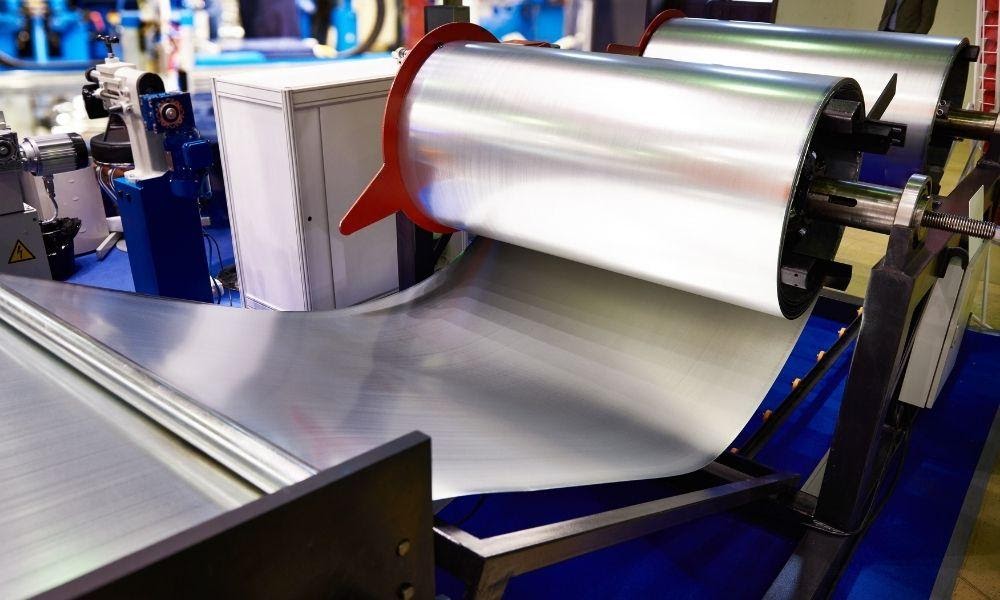
Many different metals and alloys go into manufacturing and fabricating projects. Metalworkers manipulate sheets using various complex fabrication tools and effective metal-cutting practices. The best sheet alloy or metal for metalworking projects depends on a few different factors, including the following.
- Formability
- Weldability
- Corrosion resistance
- Strength
- Weight
- Cost
The different types of sheet metal used in fabrication have varying degrees of the qualities listed above, making it imperative for fabricators to review their project requirements before purchasing or operating on metals. Metalworkers often consider the working metal type to determine which best practices for cutting sheet metal will be necessary.
Stainless Steel
Stainless steel offers varying grades for metalworkers to choose from. The most common forms of stainless steel are austenitic, ferritic, and martensitic. Discover the factors of each that sets them apart.
Austenitic
- Most widely used grade of stainless steel
- Non-magnetic
- High levels of chromium and nickel
- Low levels of carbon
- Notable for its formability and resistance to corrosion
Ferritic
- Magnetic
- Unable to be treated or manipulated with heat
- 11-30 percent chromium, little to no nickel
- Usually employed in non-structural circumstances that need quality corrosion resistance and clean aesthetics.
Martensitic
- Developed to provide a grade of corrosion-resistant stainless steel which can get worked on with heat-treating.
- Is a form of stainless steel
- Contains no nickel
Cold Rolled Steel
Cold rolled steel is fairly simple. It’s a result of metalworkers further processing hot-rolled steel to have a smooth finish and hold tighter tolerances when forming.
Pre-Plated Steel
Pre-plated steel is a product of hot-dipped galvanized steel. Metalworkers also achieve pre-plated steel by galvanizing then annealing steel, which is known as galvannealed steel.
During galvanization, metal manufacturers coat steel in zinc to curtail rust and corrosion.
Annealing alters the microstructure of a material to alter its mechanical or electrical properties, often reducing the hardness and boosting ductility.
Aluminum
Because of aluminum’s outstanding strength-to-weight ratio and natural corrosion resistance, it makes a popular sheet metal option for manufacturing sectors. Aluminum meets many manufacturing application requirements and provides ideal workability.
Aluminum sheet metal also has substantial thermal and electrical conductivity. It’s often utilized for power grid lines and transmission devices.
As you can see, each of the different types of sheet metal used in fabrication have their advantages. Each metal can be the premier choice, depending on the metalworking project at hand. Selecting the right metal is one of the first steps to ensuring a proficient fabrication job.