The Most Important CNC Maintenance Tasks
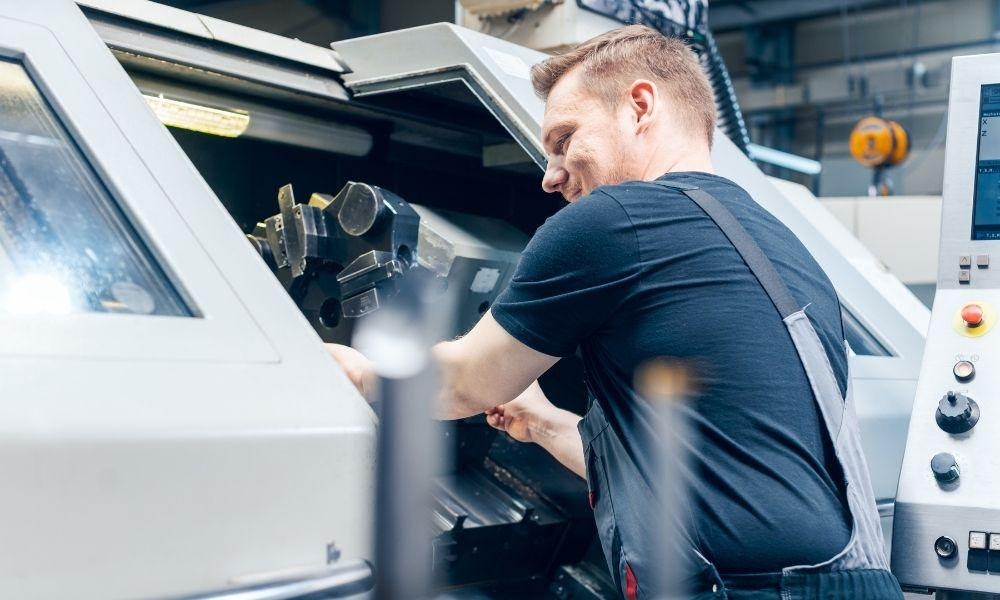
Computer numerical control (CNC) technology represents a massive improvement in the way we cut and shape materials. CNC may take much of the handiwork out of production, but the sophistication of this technology requires that the human element remain involved by diligently maintaining its operations. Here are some of the most important CNC maintenance tasks you’ll need to perform or have performed on your behalf—daily, semiannually, and annually.
What You Can Do Yourself
Some aspects of upkeep are best left to the professionals, but there’s still a sizable checklist of jobs that you as a CNC operator or manager can undertake to keep your technology working as it should. Regularly wipe down your surfaces of any residual dust or grime at least once a day. This prevents shavings from wood, plastic, or metal from infiltrating the cracks and crevasses of your mill or lathe, where they can harm delicate aspects of the machinery. You can also check the grease points of your unit and make sure those points stay well lubricated. Keep an eye on the servomotor and drive that power your spindle. If you notice something is amiss, it may be time to send it in for repairs.
Periodic Tasks for Technicians
Once every six months or after 1,000 hours of operation, whichever comes first, CNC machinery will require additional maintenance—this time in the hands of a professional specialist. Most semiannual maintenance tasks concern what’s going on under the hood, so to speak—the fluids that circulate throughout the machinery in order to keep everything fully operational. A CNC technician will examine and adjust radiator and coolant fluids, lubricants, and hydraulic fluids. This often entails a full flush of the fluids followed by replacement.
Annual Maintenance Tasks
Some of the most important CNC maintenance tasks are the ones a trained technician will perform on your behalf once a year. These are necessary tune-ups and change-outs that give your equipment a fresh start each year. These include axis adjustments, spindle alignment, and making sure both headstock and tailstock still have the proper tapering. Measuring and addressing backlash, or the loss of motion due to misaligned bearings, ensures your CNC machinery continues to operate within acceptable parameters for accuracy.