Vertere Acoustics confirms new Reference Tonearm Gen III
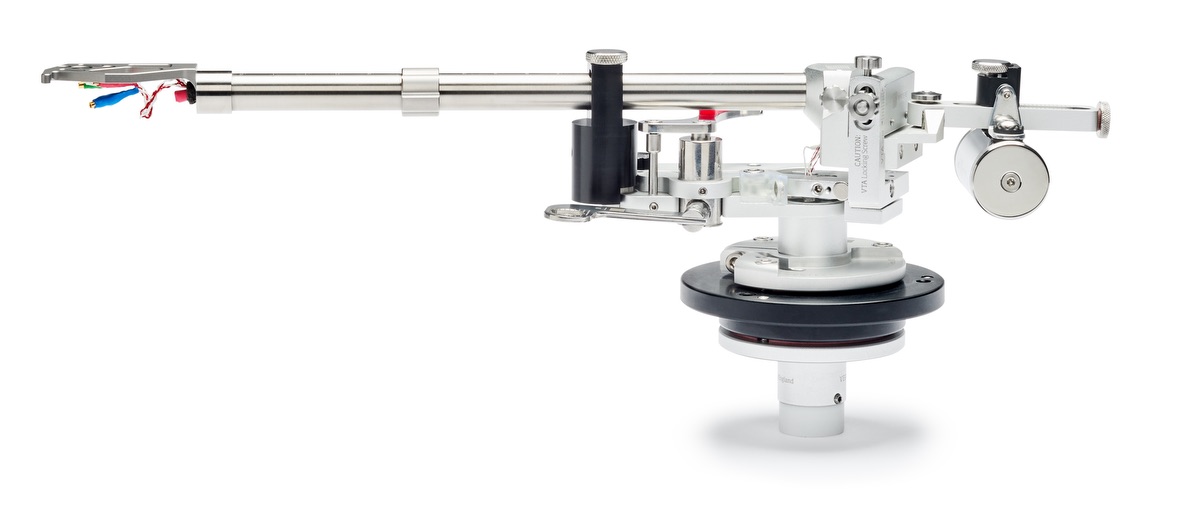
At today’spress conference at the High End Munich show at the MOC, Touraj Moghaddam, Vertere’s founder and chief designer, gave a detailed description and explanation of the new third-generation of Vertere Reference Tonearm.
Some eleven years after the launch of the original Tonearm – one that was considered genuinely revolutionary – the third generation brings additional flexibility, ease of use/fine-tuning and, of course, improved performance.
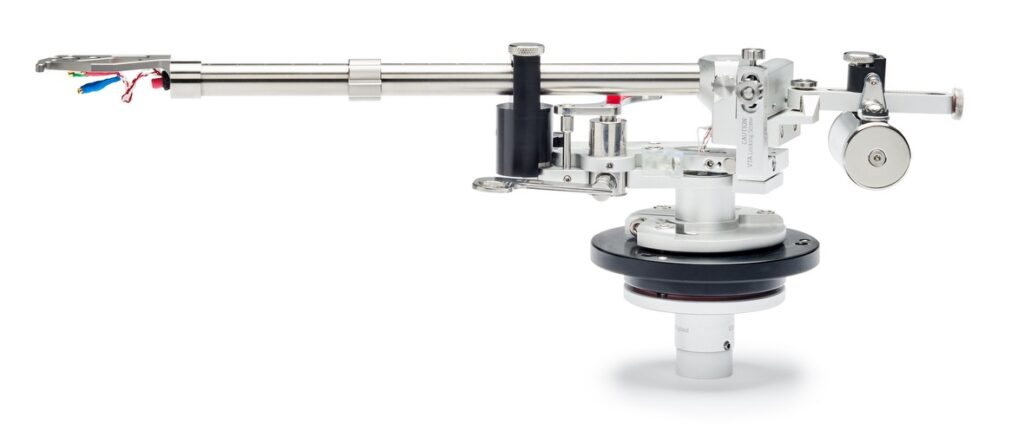
The Reference Tonearm will enhance the performance of a record playing system to a new level of resolution, clarity, dynamics, timing and sheer power that would usually be associated with live music.
As would be expected, Touraj has yet again considered zero-based engineering principles. Don’t rely on traditional hi-fi thinking but bring the design process back to solid engineering and physics with some years of experience. The Vertere Reference Tonearm is wholly engineered to give complete accuracy and certainty in cartridge setup.
The Vertere Reference Tonearm Gen III will be available shortly, in July, for £43,900, including the 1.65m HB Reference Tonearm cable
Reference Tonearm Gen III Features and Benefits
- Vertere Reference Tonearm has unique split geometry, where in the vertical direction, the arm has a longer effective length than that in the horizontal direction. This split geometry ensures that the cartridge can track very low frequencies cut in mono and the higher stereo frequencies with absolute integrity. In addition, effective mass vertically and horizontally is different, allowing optimisation of both for performance.
- Horizontal & Vertical bearings are offset by 23mm to optimise tracking accuracy and information retrieval.
- Several hundreds of micron-thick non-rotating Kevlar fibres provide the unique Vertical and Horizontal pivoting motion. The result is the first truly ‘noiseless’ and stiction-free tonearm bearing.
- This unique design has no noise-generating rotating or sliding components in the bearings.
- The counterweight assembly is fully articulated to regulate tracking weight when the record is warped – even with the slightest of up and down movements of the Tonearm (See below for a more detailed explanation). As a result, every note plays with life-like dynamics and clarity.
- Rigid, light and non‐resonant are keywords for tonearm tubes and headshells and titanium is the most suitable material. The arm tube is machined down to a mere 0.4mm in wall thickness on the reference tonearm, maximising rigidity to weight ratio. The sculpted head‐shell is then fuse-welded to the arm tube to behave as one piece. Again, this property is specific to titanium.
- The Tonearm is engraved, allowing precise setting or repeat setting of the additional sliding effective mass control/fine-tune tracking force adjustment.
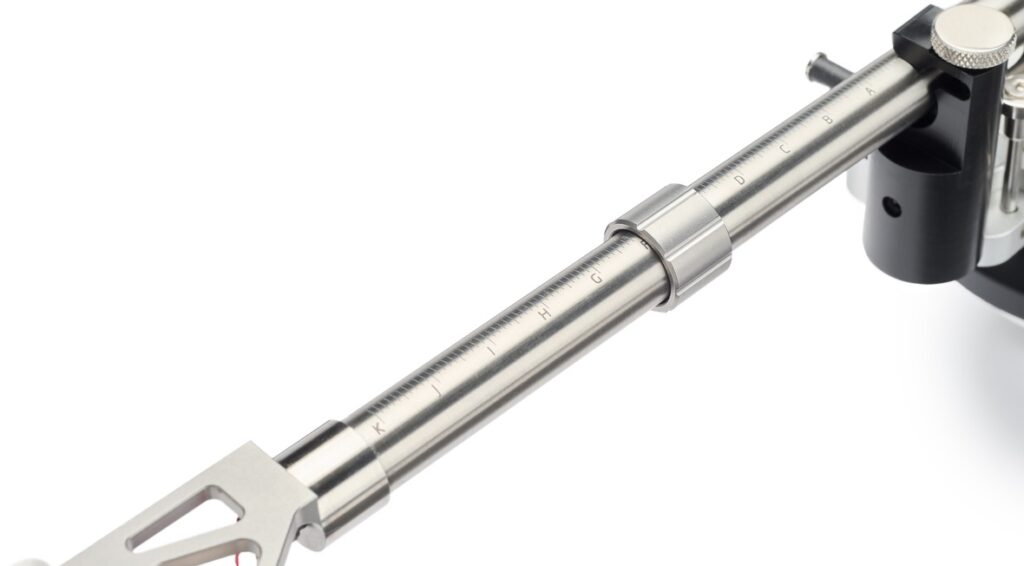
- Anti-skate force is applied using a 30 micron thick non-resonant, frictionless silicone polymer strip. Noiseless and memoryless: this is gradually counterbalanced towards the last 1/3 of the record to give the ideal non-linear anti-skate across the record playing surface. Optimal anti-skate force varies with tracking force, linear playing speed – far higher at the beginning of a record than nearing the playout area, over-hang – its effect is far higher nearing the playout area, and stylus profile, to name a few parameters.
- Unique Transit Clamping System allows secure transportation keeping the arm/cartridge safe and perfectly setup. In addition, the UTCS ensures exact performance after shipment and reinstallation. The use of the clamp also assists with mounting the cartridge safely and precisely.
- The lift/lower mechanism is custom-built from solid stainless steel and has been precision engineered to ensure smooth, firm and accurate cueing.
- Precise setting of VTA is made easy by a fine adjustment screw that’s additional to the main setting of arm pillar height.
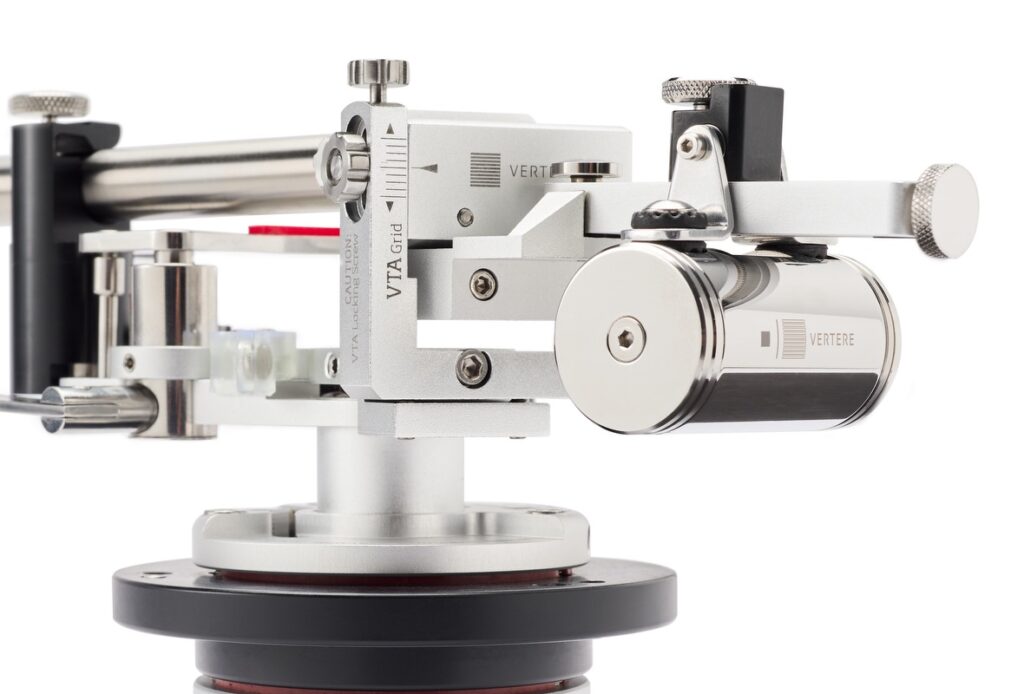
- If required, Azimuth adjustment correction is made by a side-mounted adjustment screw, while the arm mounting itself provides a very fine adjustment of azimuth.
- The Tonearm cueing light, integrated into the head-shell, is a blessing when playing records and an essential aid when setting up a cartridge. It discreetly and pleasingly illuminates the record grooves around the stylus contact point, making it easy to cue records precisely without disturbing the mood lighting. With its dedicated power supply, the light may be dimmed or switched off.
- Internal wiring is a special version of Vertere Hand-Built Pulse cable, in one continuous run from the cartridge tags to the exit cable connector at the Tonearm base. All connectors and contacts are custom made with three times the standard thickness of gold plating.
- The reference tonearm comes with a second tungsten carbide loaded Counterweight to accommodate much heavier cartridges than standard. This heavier Counterweight also has extra screw‐on end caps to increase the weight further if required.
- illuminated anti-skate dial and logos to the proprietary lift/lower mechanism and mounting plate
- Every component is custom‐built for this formidable Tonearm.
What makes the Reference Tonearm special?The ideal Tonearm would be of variable effective mass to suit whichever cartridge the owner chose and would be super rigid but without any resonances. It would be easy to setup but allow adjustment to the micromillimetre, and it would be acoustically transparent and disappear, allowing the cartridge to do its thing.Vertere Reference Tonearm with Mystic Cartridge fitted The Gen III tonearm is close but still no cigar. The effective mass is adjustable, the titanium headshell and arm tube are super-stiff but have no apparent resonances, and every aspect of the setup is easy and repeatable. Some might be describing the Gen III as the ultimate in flexibility and almost the Universal Tonearm, but it has one drawback: it’s not ideal for use with high compliance cartridges.The key, though, is in the listening: mount the Reference to a good Turntable (Vertere SG-1 or RG-1 suggested), set it up with a good cartridge (again Vertere Mystic suggested) and enjoy. Like all Vertere products, it is not ‘dramatically’ spectacular. It’s the music, the emotions and the resolution it drags from the groove that is spectacular. |
More detailed explanationsAs the cartridge tracks the record, it also has to move the Tonearm, side to side and up and down. It does this to position itself, as closely as possible, on the mean line of the groove. Failure to do this accurately will result in loss and distortion of the musical signal the cartridge is to extract. |
Technical SpecificationsType Pivoted Effective Length 240mm Horizontal 263mm Vertical (Effectively) Overhang 17.5mm Offset Angle 22.9° Head-Shell & Arm Tube Titanium & Titanium – Fuse Welded Fine Tracking Force Adjustment Weight Titanium – 3.2g Bearing Yoke Structure Aluminium Alloy BodyTitanium Insert Bearing Type Non-Rotating microns-thick Kevlar thread Fibres Counter Weight Stainless (Standard) + End DiscsStainless & Tungsten Carbide (Heavy) + End Discs Articulated Triple Ball Races Counter Weight System Articulated – Three Ball Races Internal Wiring Special Hand-Built Pulse Signal & LED Power Wiring Connector Proprietary Cartridge & Cable Connectors Triple-thickness Gold Plated Contacts Vertere 7-Way Tonearm Connector Tonearm Cable Special Pulse-HB Hand-built Triple-thickness Gold Plated Contacts Vertere HB Reference 23.95ct Gold/5 micron+ Queuing Light Power Supply Dimmable – Battery Powered Standard Counterweight (x1) 142g Standard C/W Disc (x6) Each 7.6g Heavy Counterweight Sleeve (x1) 83g Tungsten Carbide C/W Insert (x1) 114g Special C/W Disc (x4) Each 7.6g Overall Weight (With Std C/W & x4 Discs) Approx. 627g |
Some backgroundAs with virtually every aspect of hi-fi design, tens of thousands of words have been written and often quoted verbatim, justifying a particular aspect of a design. A good example is tonearm bearings, with the common belief that ball races offer the best solution to quiet bearings with swing tests and other public displays given to show efficacy. First, we should revisit first principles and consider the priorities for the bearing. Low noise will be high on the list but perhaps behind low friction and, even more, important low-to-zero stiction. Here there is a dichotomy with ball races: the tighter they are set to give the least bearing rattle, the higher the friction and stiction with yet higher ball race ‘sliding’ noise. The question should be: do the bearings dictate rigidity to preserve the signal, or should their first priority be to the cartridge and record and hence go where they are told to go? The proof is in the listening.Touraj explains the source of some of his background knowledge“Our collaboration with music industry engineers has given us invaluable insights into the art of cutting. This knowledge has enabled us to advance our record player design in many ways to extract the maximum from vinyl records.For example, with his recent remixes of the Beatles albums, Giles Martin – son of the late Sir George – used a Vertere MG-1 record player, including SG-1 tonearm and PHONO-1 preamplifier throughout, to check and approve the acetates and the test pressings.And we’ve worked closely with the multi-award-winning mastering engineer Miles Showell: since February 2017.Miles has been using his own extensively customised Neumann VMS 80 lathe, incorporating Vertere cables, to cut normal and half-speed masters for the likes of ABBA, Cream, The Police and The Rolling Stones, and also the 50th-anniversary release of The Beatles’ Sgt Pepper’s Lonely Hearts Club Band and The Beatles (otherwise known as ‘The White Album’).Working closely with Mileshas led to the first releases on our record label Vertere Records. Releases: a three-track EPand first albumby Scottish band Caezar, and the first album by Dutch singer/songwriter Elles Springs, which was specially tape-transferred and then half-speed mastered and cut by Miles for our label.It’s only by involving ourselves at every stage of the record-making process that we can ensure our players bring you as close as possible to what the artists and engineers wanted you to hear.”About VertereReducing engineering to its fundamentals, to get you even closer to the original recording.When aiming to reproduce the complexities of music, it’s all too easy to introduce even more significant complication in the engineering of audio equipment, putting in place one element to solve the problems until the whole design escalates into something fiendishly intricate – and expensive.That’s not the Vertere way: coming at the whole problem with decades of audio and mechanical engineering experience, plus close collaboration with the recording and mastering industry, we step back, take a long hard look at the fundamentals, and look for simple, elegant solutions.That may sound like a simple ‘less is more’ philosophy, but we prefer to look at it this way: the best audio equipment shouldn’t add anything to or remove anything from the original recording. Instead, it should affect it as little as possible; bringing the listener ever closer to what the artist, producer and mastering engineer wanted you to hear. |