What Causes Weld Spatter & How Do You Reduce It?
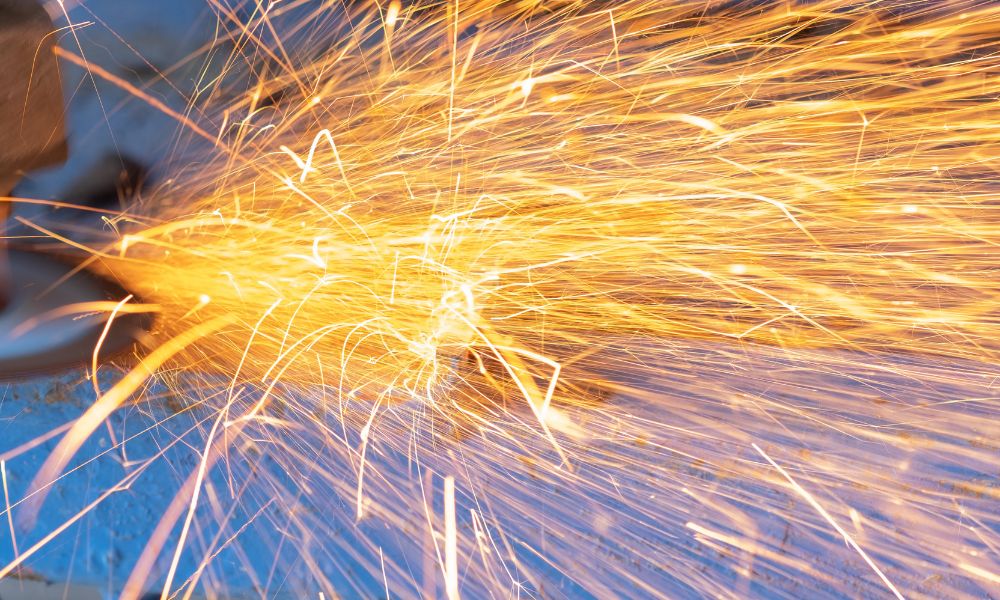
Nothing is more frustrating than finishing up a welding project only to realize tiny beads are melted to it. In this article, we go over what causes weld spatter and how you can reduce it. This will help you create cleaner welds that are both durable and strong by learning how to avoid this specific welding defect.
What Is Weld Spatter?
Weld spatter is one of the common welding defects you must avoid. This defect comes from scorching-hot molten droplets of metal that splatter from a weld pool. These beads can attach to anything nearby, including your weld tools, project, or even you. Ejecting metal from your weld in the form of spatter could weaken your project. Learning how to avoid or fix this issue will ensure that the integrity of the weld stays intact throughout the process.
What Causes Weld Spatter?
Generally, anything that disrupts the weld pool can spray the molten droplets out of the weld. Commonly, these are due to the welding technique, material composition, contamination, welder settings, or equipment issues. For example, a classic cause of weld spatter is when you transfer a wire into the weld. The incentive for the disturbance with the wire is usually caused by the amperage and voltage settings on your tools.
Now that you understand what can cause weld spatter, let’s take a look at how you can reduce it.
How To Avoid or Reduce Weld Spatter
First, what kind of filler material are you using for your weld? The quality of your materials matters tremendously because cheaper fillers can produce more spatter. Choose a high-quality filler material to avoid disturbing or splattering the weld pool. To avoid spatter due to contamination, clean both sides of the weld with a metal brush to remove any rust or dirt.
Changing the weld settings for MIG or TIG welding is essential for reducing spatter. For MIG, the components to double-check are the polarity of the tool, using the correct wire, voltage with sufficient heat, and a wire speed suitable for your requirements or skills. For TIG, you should make sure that your travel speed is not too fast for your weld and that a current or voltage setting is not too hot or cool.
Overall, you can reduce spatter by gaining more experience by practicing your skills and technique. This welding defect has many causes, so it’s important that you understand each one and how to fix it to create a durable weld. Always check the settings on your equipment and ensure you’re using the correct methods for your project.