The Importance of Proper Layout Design in Piping Systems
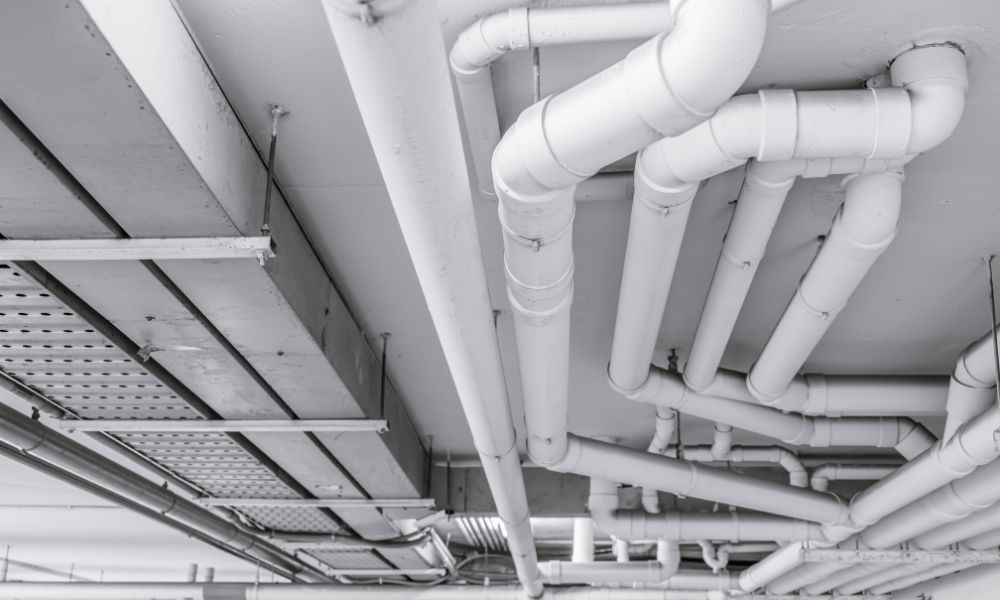
Manufacturing and industrial facilities can use a lot of pipes—sometimes miles of them. A strategic layout contributes significantly to the system’s efficiency, longevity, and ease of maintenance. Moreover, a piping system’s design directly impacts the cost and timeline of installation. Learn more about the importance of proper layout design in piping systems.
Consider the Contractor
It’s unlikely that an industrial facility will employ the personnel necessary to install a complex piping system full time. The facility owners and managers will hire a contractor to do the work. That means that one of the first steps in designing a piping system is to consider the contractor’s capabilities and resources.
The piping system’s layout should align with the chosen contractor’s skills and available equipment. A design that’s too complex may lead to installation errors if the contractor doesn’t have the necessary expertise or tools. Similarly, an expert contractor can point out potential flaws or issues in the system’s design that could affect its operational efficiency or safety. Clear and effective communication between the designer and contractor becomes vital for a successful piping system installation project.
Plan for Imperfections in the Installation Site
Every installation site presents its unique set of challenges. Obstacles or limitations, such as existing structures, underground utilities, large machinery, imperfect walls, or natural features like rocks and slopes can influence pipe routing. Anticipating these imperfections in advance aids in preventing delays and additional costs during the installation phase.
Vertical vs. Horizontal Layouts
Choosing between vertical and horizontal layouts depends on factors like space availability, the substance that will flow through the system, and the operational requirements of the facility. Vertical layouts are preferable in high-rise buildings or areas where space is a constraint. Horizontal layouts are common in industrial applications where manufacturing and production facilities spread out over a large area. Each layout type comes with its own set of challenges and benefits, making the choice highly dependent on the specific needs of the project.
Think About Future Modifications When Placing Valves
Valves play a pivotal role in controlling the flow within a piping system. While placing valves, consider potential future modifications to the system. For instance, if there’s a possibility of expanding the system in the future, it may be prudent to position valves in locations that facilitate easy extension of the pipework or relocation of valves.
Try for Straight Lines Wherever Possible
Straight pipe runs are typically more efficient and easier to install and maintain. However, situations arise where pipes must change direction or navigate corners and curves. In these cases, different types and sizes of elbow fittings may be necessary.
Elbow fittings assist in managing directional changes while minimizing the impact on pressure and flow. It’s essential to choose the right type of elbow fitting based on the degree of change in direction required and the characteristics of the fluid the pipes must transport. Also, note the flow and pressure the system must maintain.
Designing a proper piping system layout requires careful consideration of practical factors like the nature of the installation site, the contractor’s capabilities, the amount of space available, and the media that will flow through the system. Thoughtful design can extend the system’s useful life, reduce maintenance costs, and contribute to efficient operation of industrial and manufacturing facilities.