3 Effective Ways To Measure Your Manufacturing Productivity
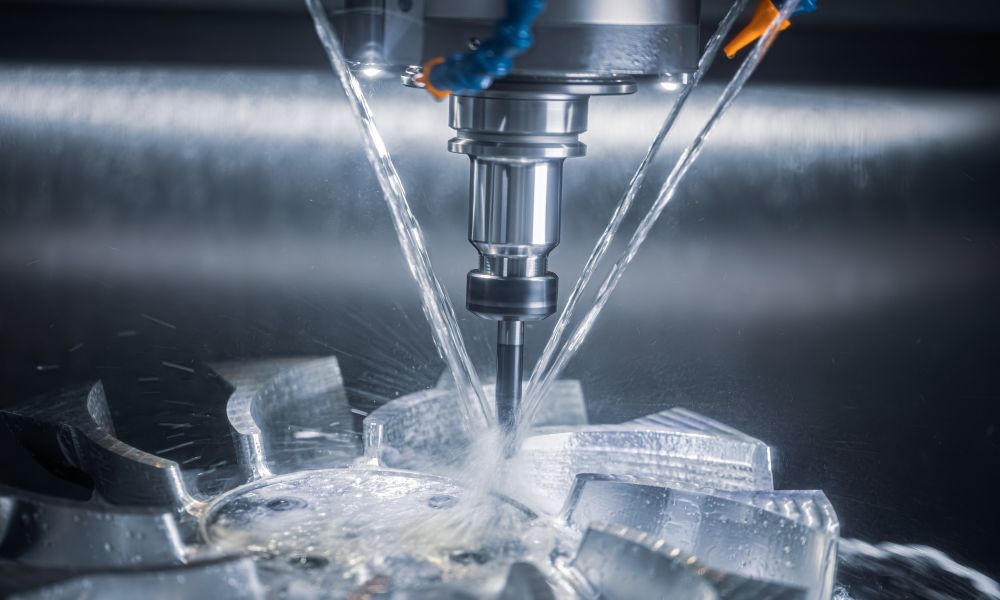
For manufacturing managers and business owners, productivity measurement is akin to the compass that guides their operations to success. Your equipment can be state of the art, and your workforce can be highly skilled, but without accurate performance tracking, you’re navigating blind. Investigate three of the most effective ways to measure your manufacturing productivity to keep your output consistently reliable.
Overall Equipment Effectiveness (OEE)
OEE is a widely recognized metric that evaluates the productivity of plant machinery. It provides a complete picture of how effectively each machine is running by combining data on availability, performance, and quality. OEE is like having three performance metrics in one, making it incredibly powerful for gauging your equipment’s profitability.
The ratio of run time to planned production time is what measures availability. It’s essentially a measurement comparing the operational time of a machine against its downtime, such as for mechanical breakdowns or planned maintenance.
Performance is the ratio of actual running speed to the ideal speed, including any small stops or speed losses. Quality measures the number of good parts produced against the potential parts produced. Suffice it to say consistent quality is key.
Labor Productivity
Labor accounts for a significant portion of manufacturing costs, so it makes sense to measure its productivity. An effective way to do so is by calculating the output of the manufacturing process per person over a specific period. It’s a direct line to assessing workforce efficiency and ensuring that your most valuable assets, your employees, are working at peak performance.
Assessing this data is key to finding operational bottlenecks and opportunities for technique or technological innovation.
For instance, understanding how to increase manufacturing throughput with CNC machining is crucial for identifying an opportunity to maximize productivity while producing quality products. Looking closer at your operation means you can look ahead and upgrade your practices accordingly. Understanding how to use your labor most efficiently not only reduces costs but also enhances output.
Defect Rate
Defects can lead to scrap, rework, or even liability costs. Monitoring defect rates is fundamental to controlling quality and production costs. Reducing defects improves quality and frees capacity, driving cost savings and enhancing customer satisfaction.
To monitor defect rates effectively, establish clear thresholds and regular inspection cycles. Investing in quality-control tools and training your staff to perform root-cause analysis can dramatically reduce the incidence of defects.
Don’t let avoidable problems hold your production back. Remember these critical ways to measure your manufacturing productivity so that you can enhance your workforce immediately.