Mitigating Corrosion in Petroleum Refining Processes
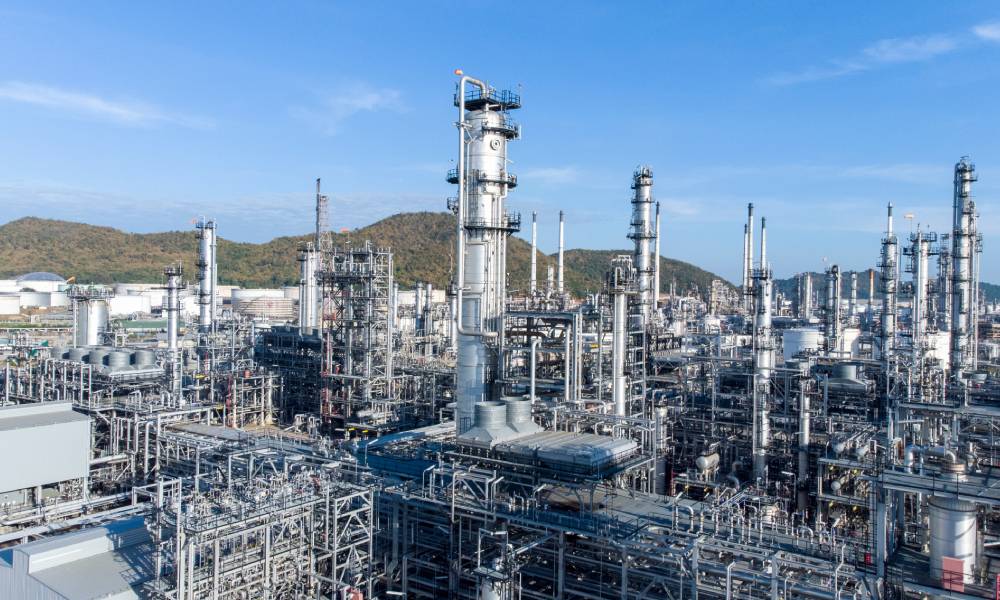
Understanding the implications of corrosion in petroleum refining is crucial for professionals in the plastic manufacturing sector. This is because the quality and consistency of petroleum-based feedstocks directly affect the production processes and final quality of plastic products. Read on to learn more about effectively mitigating corrosion in petroleum refining processes.
Understanding Corrosion in Petroleum Refineries
Corrosion in petroleum refineries can manifest in various forms, deeply affecting operations and safety. Sulfidation, a direct consequence of the reaction between sulfur compounds in crude oil and refinery materials, is particularly prevalent. It often leads to the degradation of carbon steel materials at high temperatures. Similarly, stress corrosion crackingposes a significant threat, where mechanical stress in the presence of a corrosive environment leads to cracking and eventual failure of components. Other types include naphthenic acid corrosion and corrosion under insulation. The former occurs due to the acid content in crude oils reacting with the steel. The latter is a deceptive type that develops unseen under the insulation material of pipework and equipment, making it difficult to detect and address promptly.
Current Challenges in Corrosion Mitigation
One of the principal challenges in mitigating corrosion within the petroleum refining industry is the early detection and accurate diagnosis of corrosion types. Various corrosive agents and operational conditions unique to each refinery complicate identifying and implementing effective countermeasures. Furthermore, the economic cost associated with corrosion prevention includes investment in corrosion-resistant materials and technologies. High temperatures, extreme pressures, and the corrosive nature of the feedstock exacerbate the situation. They necessitate continuous research and development efforts to innovate more effective and cost-efficient solutions.
Solutions for Corrosion Control
One foundational approach to combat corrosion in petroleum refineries involves using corrosion-resistant materials. These include stainless steel, alloy composites, or nonmetallic alternatives for pipelines, vessels, and other critical refinery components. Additionally, applying protective coatings and liners offers another layer of defense, shielding the underlying material from corrosive substances. These coatings withstand the harsh chemical environments in petroleum refining processes, prolonging the lifespan of the equipment.
Another critical strategy for corrosion mitigation hinges on the continual monitoring and maintenance of refinery infrastructure. Implementing advanced corrosion monitoring technologies, such as ultrasonic thickness gauging and corrosion probes, allows for the real-time assessment of equipment integrity, enabling timely interventions before significant damage occurs. Ultrasensitive pressure transducers can monitor pressure levels inside your refining equipment to reduce stress-related corrosion. As with your piping and vessel walls, consider an anti-corrosive material when choosing a pressure transducer for your application.
Mitigating corrosion in petroleum refining processes ensures the longevity and efficiency of refinery operations and significantly contributes to the petroleum industry’s safety and economic sustainability. Importantly, less corrosion in petroleum refining processes leads to better plastic products in manufacturing and production.