Maintenance Tips for Mechanical Power Generation Equipment
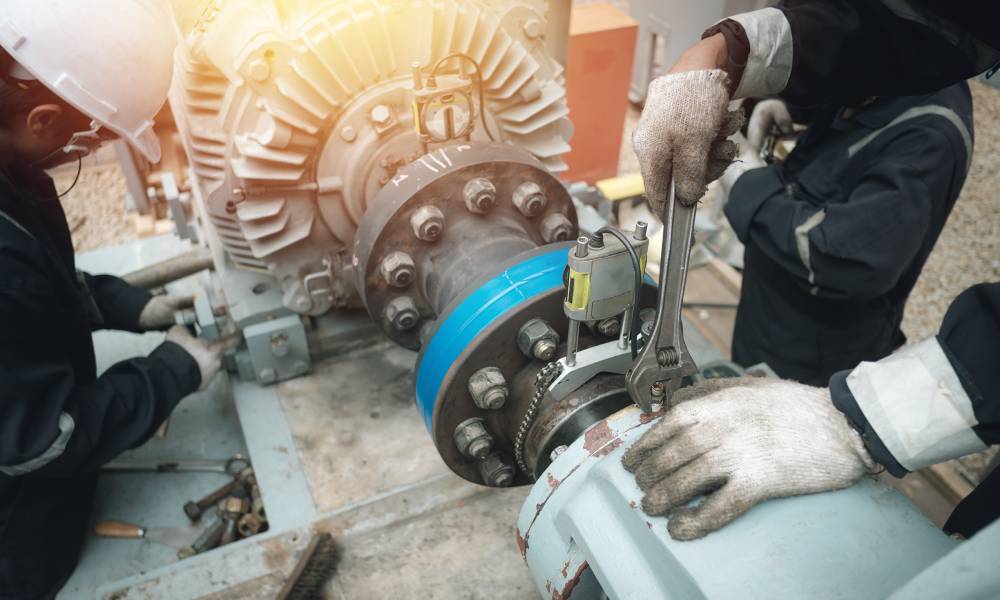
Proper maintenance of mechanical power generation equipment is crucial for ensuring operational efficiency, longevity, and safety. Whether you’re managing large-scale industrial facilities or smaller, localized equipment, regular maintenance can prevent costly breakdowns and unscheduled downtimes. For industries relying heavily on a continuous power supply, a well-maintained system enhances performance and guarantees reliability and compliance with safety standards. Read on to discover three key maintenance tips for mechanical power generation equipment.
Tip I: Regular and Proper Lubrication
Lubrication plays a pivotal role in the maintenance of mechanical power generation equipment, particularly for components such as ball bearings. Regular and proper lubrication minimizes friction and wear, ensuring the ball bearings operate smoothly and efficiently. Without adequate lubrication, ball bearings can experience excessive heat buildup, leading to premature failure and significant damage to the equipment. Proper lubrication helps distribute heat evenly and reduces the risk of metal-to-metal contact, extending the lifespan of the bearings and maintaining operational continuity.
In addition to ball bearings, other components like gears, shafts, and pulleys also benefit from regular lubrication. These parts are subject to constant motion and loads, making them susceptible to wear and tear. By adhering to a scheduled lubrication regimen and using the recommended lubricants, you can prevent corrosion, contamination, and mechanical failures. Furthermore, proper lubrication contributes to the overall energy efficiency of the system, reducing power consumption and operational costs.
Tip II: Scheduled Inspections
Scheduled inspections are vital for the maintenance of mechanical power generation equipment, as they provide an opportunity to identify and address potential issues before they escalate into significant problems. By following a consistent inspection schedule, maintenance personnel can systematically assess the condition of various components, ensuring that any necessary repairs or adjustments occur promptly. This proactive approach not only prolongs the lifespan of the equipment but also prevents unplanned downtimes and costly repairs. Furthermore, scheduled inspections contribute to compliance with industry safety standards and regulations, ensuring a safer working environment for personnel and the consistent reliability of the power generation system.
Tip III: Robust Training and Record Documenting
Proper training for personnel involved in the maintenance of mechanical power generation equipment is indispensable for ensuring that the equipment receives effective and safe servicing. Staff should be well-versed in the operational aspects of the equipment, as well as in the specific maintenance procedures and safety protocols. Alongside robust training, meticulous record-keeping of all maintenance activities is crucial. Documenting inspections, lubrication schedules, and any repairs carried out helps track the equipment’s history and identify recurring issues. This data-driven approach enables more informed decision-making and facilitates predictive maintenance strategies, ultimately enhancing the power generation system’s reliability and efficiency.
The role of a facility manager isn’t always easy, but your responsibilities for maintaining the entire plant are indispensable for productivity and efficiency! From knowing how to install a shaft-mounted speed reducer to understanding the ongoing maintenance requirements for that same equipment, you must be familiar with your facility inside and out. Follow these maintenance tips for mechanical power generation equipment to ensure your facility is functioning at peak efficiency!