NASA Marshall Engineers Unveil Versatile, Low-cost Hybrid Engine Testbed
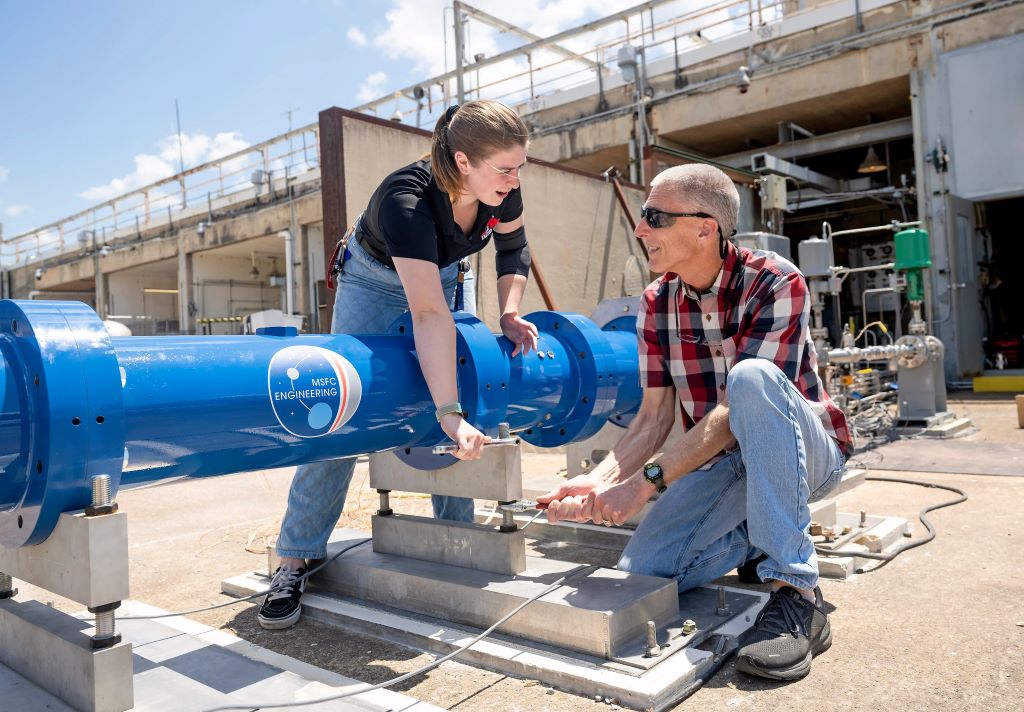
In June, engineers at NASA’s Marshall Space Flight Center in Huntsville, Alabama, unveiled an innovative, 11-inch hybrid rocket motor testbed.
The new hybrid testbed, which features variable flow capability and a 20-second continuous burn duration, is designed to provide a low-cost, quick-turnaround solution for conducting hot-fire tests of advanced nozzles and other rocket engine hardware, composite materials, and propellants.
Solid rocket propulsion remains a competitive, reliable technology for various compact and heavy-lift rockets as well as in-space missions, offering low propulsion element mass, high energy density, resilience in extreme environments, and reliable performance.
“It’s time consuming and costly to put a new solid rocket motor through its paces – identifying how materials perform in extreme temperatures and under severe structural and dynamic loads,” said Benjamin Davis, branch chief of the Solid Propulsion and Pyrotechnic Devices Branch of Marshall’s Engineering Directorate. “In today’s fast-paced, competitive environment, we wanted to find a way to condense that schedule. The hybrid testbed offers an exciting, low-cost solution.”
Initiated in 2020, the project stemmed from NASA’s work to develop new composite materials, additively manufactured – or 3D-printed – nozzles, and other components with proven benefits across the spacefaring spectrum, from rockets to planetary landers.
After analyzing future industry requirements, and with feedback from NASA’s aerospace partners, the Marshall team recognized that their existing 24-inch rocket motor testbed – a subscale version of the Space Launch System booster – could prove too costly for small startups. Additionally, conventional, six-inch test motors limited flexible configuration and required multiple tests to achieve all customer goals. The team realized what industry needed most was an efficient, versatile third option.
“The 11-inch hybrid motor testbed offers the instrumentation, configurability, and cost-efficiency our government, industry, and academic partners need,” said Chloe Bower, subscale solid rocket motor manufacturing lead at Marshall. “It can accomplish multiple test objectives simultaneously – including different nozzle configurations, new instrumentation or internal insulation, and various propellants or flight environments.”
“That quicker pace can reduce test time from months to weeks or days,” said Precious Mitchell, solid propulsion design lead for the project.
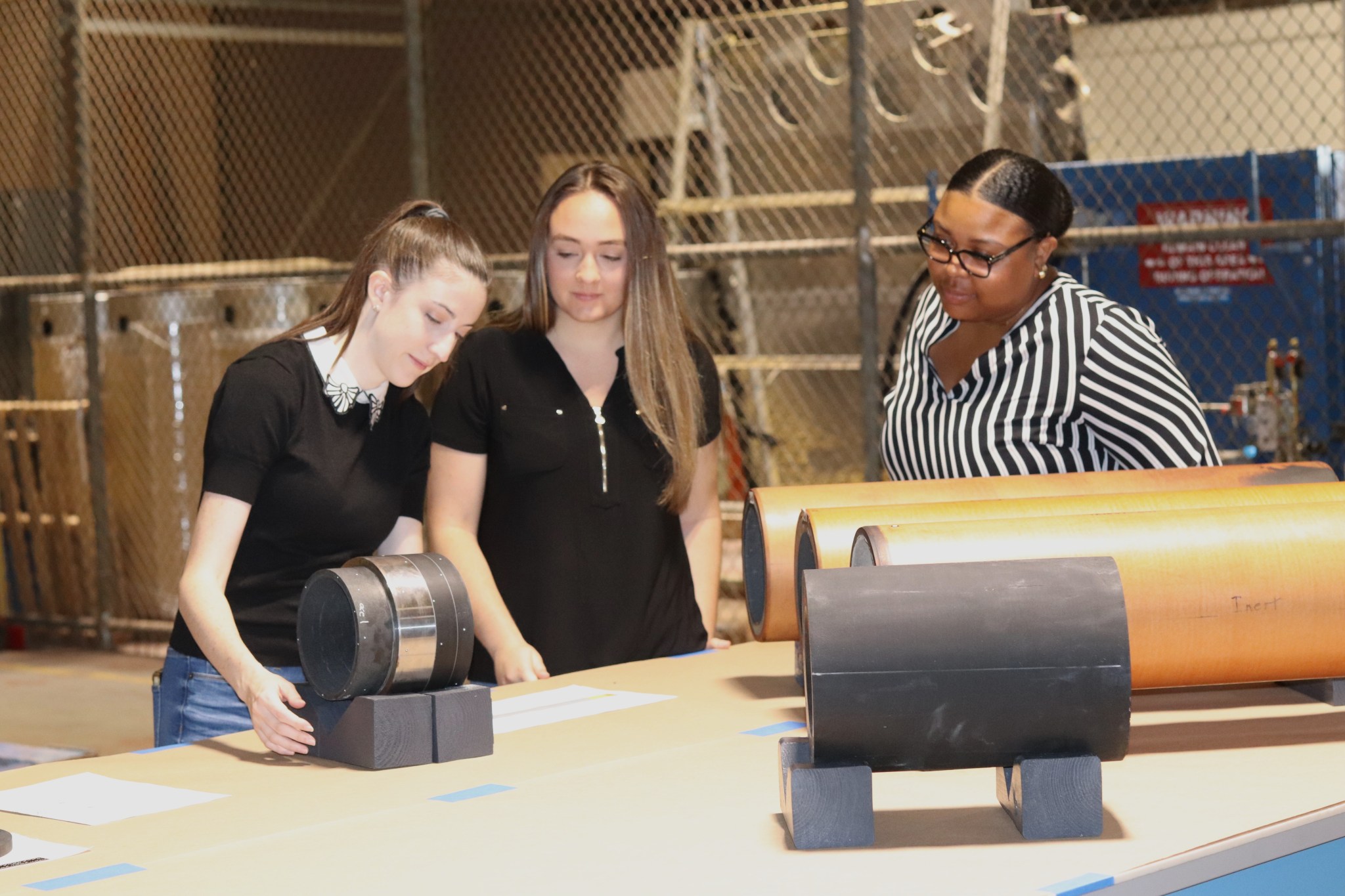
Engineers at NASA’s Marshall Space Flight Center in Huntsville, Alabama, assess components of the 11-inch hybrid rocket motor testbed in the wake of successful testing in June. Among Marshall personnel leading in-house development of the new testbed are, from left, Chloe Bower, subscale solid rocket motor manufacturing lead; Jacobs manufacturing engineer Shelby Westrich; and Precious Mitchell, solid propulsion design lead.
NASA/Benjamin Davis
Another feature of great interest is the on/off switch. “That’s one of the big advantages to a hybrid testbed,” Mitchell continued. “With a solid propulsion system, once it’s ignited, it will burn until the fuel is spent. But because there’s no oxidizer in hybrid fuel, we can simply turn it off at any point if we see anomalies or need to fine-tune a test element, yielding more accurate test results that precisely meet customer needs.”
The team expects to deliver to NASA leadership final test data later this summer. For now, Davis congratulates the Marshall propulsion designers, analysts, chemists, materials engineers, safety personnel, and test engineers who collaborated on the new testbed.
“We’re not just supporting the aerospace industry in broad terms,” he said. “We’re also giving young NASA engineers a chance to get their hands dirty in a practical test environment solving problems. This work helps educate new generations who will carry on NASA’s mission in the decades to come.”
For nearly 65 years, Marshall teams have led development of the U.S. space program’s most powerful rocket engines and spacecraft, from the Apollo-era Saturn V rocket and the space shuttle to today’s cutting-edge propulsion systems, including NASA’s newest rocket, the Space Launch System. NASA technology testbeds designed and built by Marshall engineers and their partners have shaped the reliable technologies of spaceflight and continue to enable discovery, testing, and certification of advanced rocket engine materials and manufacturing techniques.
Learn more about NASA Marshall capabilities at:
https://www.nasa.gov/marshall-space-flight-center-capabilities