Controlled Propulsion for Gentle Landings
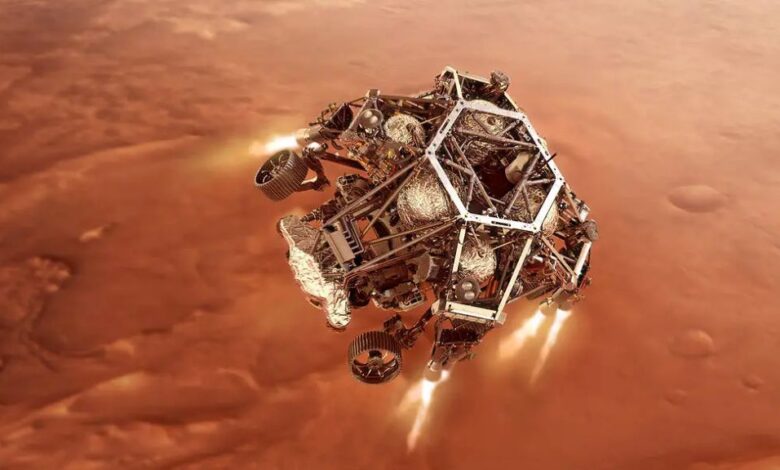
A valve designed for NASA rover landings enables effective stage separations for commercial spaceflight
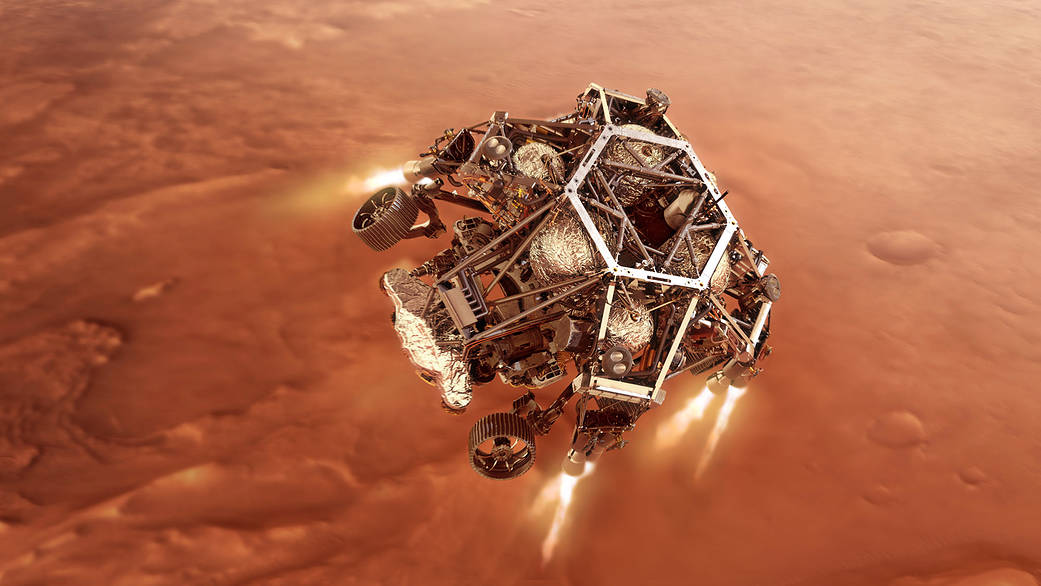
The controlled descent of the Mars Curiosity rover included the use of propulsion rockets pointing to the surface to allow a gentle landing. The engine, shown firing in this illustration of Perseverance and the sky crane landing system relied on a pyrovalve that released the rocket fuel.
Credit: NASA /JPL-Caltech
The Curiosity and Perseverance Mars rovers continue to provide a wealth of information about the Red Planet. This was made possible in part by the sky crane landing systems that safely lowered them to the planet’s surface. Their successful descent, managed by eight powerful engines, depended on one small part – a valve.
The engines produced about 750 pounds of thrust each, so they required more fuel than a conventional valve could deliver, said Carl Guernsey, propulsion subsystem chief engineer for the Mars Sample Laboratory Mission.
“With the engines pointing down, we throttle up and increase the thrust, so we slow down,” said Guernsey. “At a certain altitude above the surface, you hold at a constant velocity to collect more sensor data, and then proceed with the rest of the descent.”
With only seconds for sensor data to identify the landing area and direct any last-minute diversion maneuvers, landing requires fuel available at the right time. To build the valve to help accomplish this task, NASA turned to a company that has provided the space program with reliable gas regulators since the 1950s. Through a series of mergers, by 2021, the original company, called Conax Florida, became part of Eaton based in Orchard Park, New York.
Working under contract with NASA’s Jet Propulsion Laboratory in Southern California, the company developed a new one-time-use pyrovalve to sit between the hydrazine fuel tank and engines. The zero-leak valve was the largest ever made of its type at the time, at three-fourths of an inch.
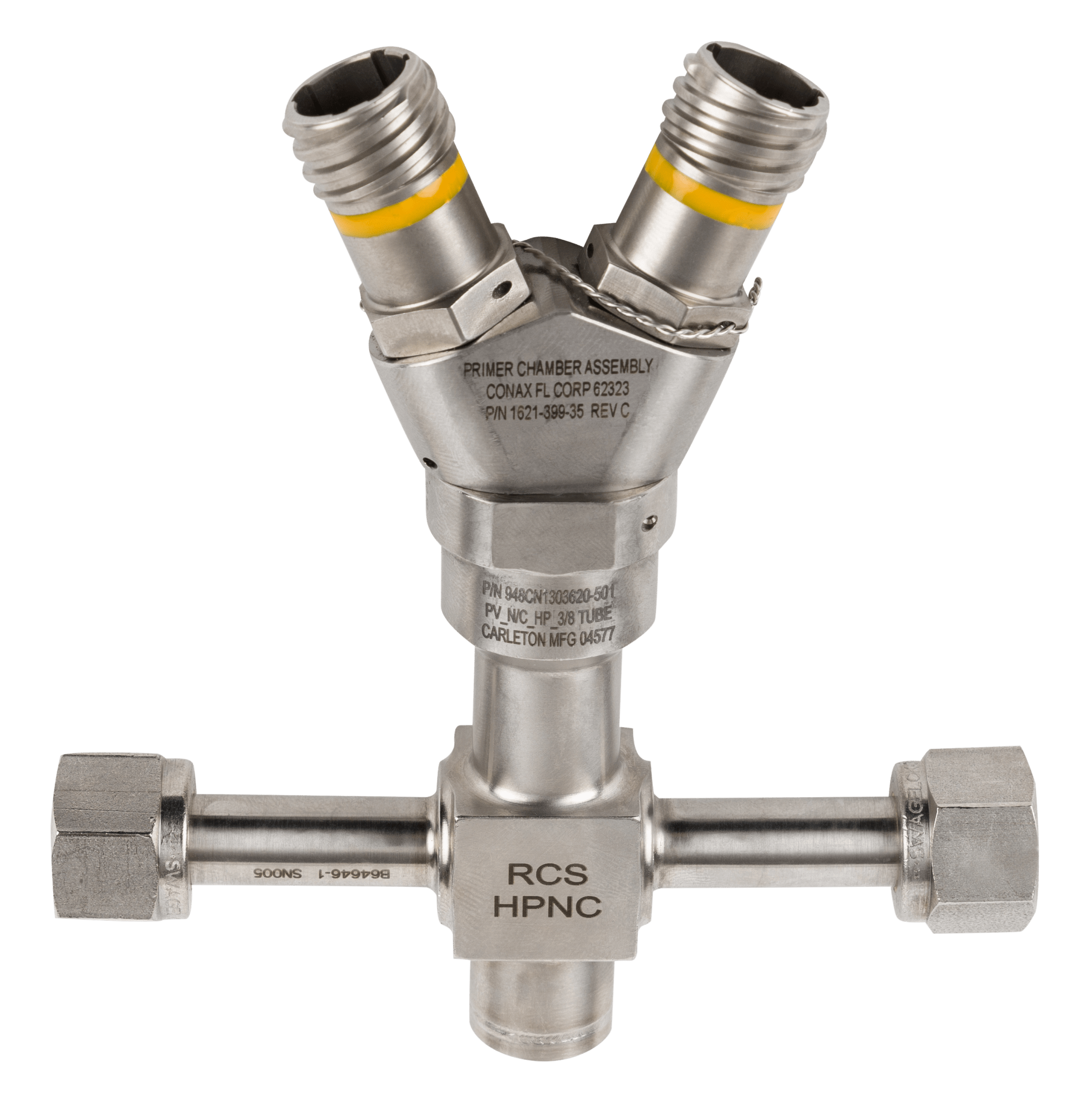
This one-time-use pyrovalve sat between the hydrazine fuel tank and the controlled-descent engines on the sky crane for the Curiosity and Perseverance Mars rovers. The zero-leak valve developed by Eaton also ensured no fuel was lost on the long flight to Mars.
Credit: Eaton Corp.
The Y-shaped pipe with a pair of leak-proof solid metal barriers prevented propellant from flowing. The valve contains a pyrotechnic charge that activates a piston called a flying ram, which shears off the barriers, allowing fuel to flow. But a problem arose during flight qualification testing. Sometimes the ram didn’t stay wedged in place at the bottom, posing a blockage risk.
The solution the team came up with had never been tried before – magnets at the bottom of the valve. But the successful Perseverance landing in 2021 proved it works. The same valve is included in the Perseverance rover and now enables commercial rocket-stage separation in space.