How Frequently Should You Lubricate Industrial Machines?
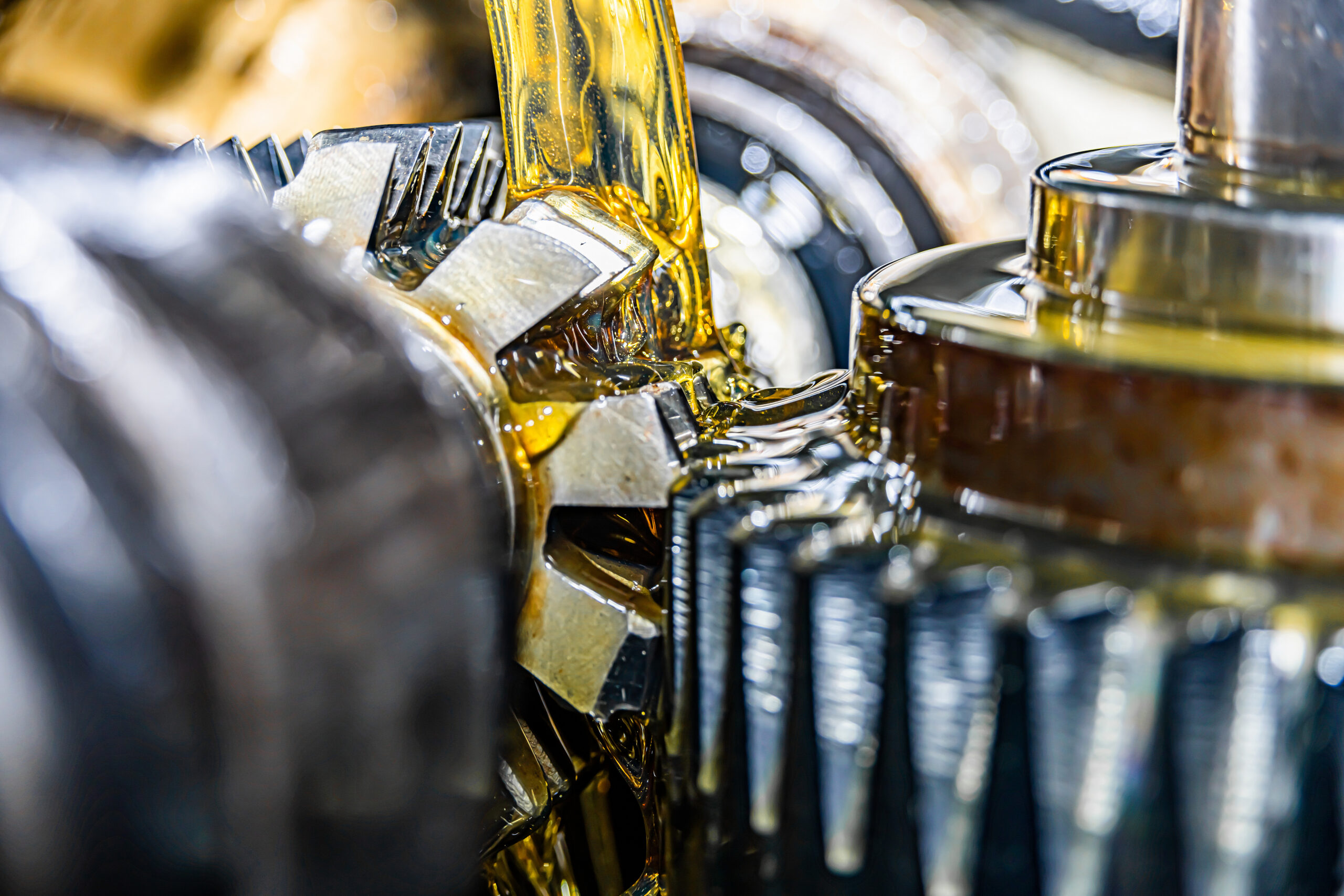
A well-oiled machine runs smoother, lasts longer, and produces better results. Neglect lubrication, however, and you’re inviting wear, inefficiency, and costly downtime into your operations.
But the question remains—how often should you lubricate industrial machines? Use this guide to break down everything you need to know, from identifying warning signs to understanding lubrication intervals and best practices.
Why Lubrication Is Nonnegotiable
Lubrication plays a critical role in reducing friction and wear between moving components, which, in turn, minimizes heat generation and energy loss. Well-lubricated machinery operates more efficiently, consumes less power, and is significantly less prone to breakdowns. This single maintenance task, when done right, saves companies thousands of dollars annually.
Signs Your Machinery Needs Lubrication
While following a predetermined lubrication schedule is vital, you may experience instances where machines give off tell-tale signs they need attention. Odd noises, such as grinding or squeaking, often suggest that parts are rubbing together without enough lubrication.
Overheating components are another common symptom, as friction generates heat when lubrication is lacking. Vibration or excessive wear, spotted during routine inspections, also indicates that the lubricant might be insufficient or improperly applied. Monitoring these signs ensures that you act before minor issues escalate into major problems.
How Often Should Different Machines Be Lubricated?
The lubrication frequency for industrial machines is not one-size-fits-all. Equipment types, usage levels, operational environments, and lubricant specifications all play a role. Heavy-duty machines running continuously in outdoor or high-moisture conditions often require lubrication daily or weekly to counter environmental stressors.
Conversely, low-intensity machines operating in controlled environments might only need lubrication monthly or quarterly. Consult the equipment manufacturer’s manual for guidance, as it will detail the recommended intervals for optimal performance. Maintenance logs also serve as a practical reference to track wear patterns and adjust schedules based on real-world usage.
What Type of Lubricant Should You Use?
Choosing the right lubricant is just as critical as applying it regularly. Grease, oil, and synthetic lubricants each suit different machinery and operating conditions. For example, oil tends to be ideal for high-speed machines like conveyors, while grease works better for heavy-load equipment such as bearings and gearboxes.
Synthetic lubricants offer enhanced benefits, like higher temperature tolerance, and are best for modern machinery under intense workloads. Always match the lubricant’s viscosity and formulation to the machine’s requirements to prevent damage.
Tips for Lubrication and Maintenance Schedules
Create a detailed maintenance schedule to ensure all machines receive care. Various parts of your machines require frequent attention, such as the motor. Regular inspections are one of the most common maintenance strategies for industrial electric motors to ensure machines run at their best.
Alongside manual inspections, preventive maintenance software sets reminders and manages lubrication intervals systematically. Conduct training programs for your maintenance staff to ensure they understand the correct lubrication techniques, including the amount to be applied and the application process. Over-lubricating is just as harmful as under-lubricating, leading to issues like seal damage or excess lubricant attracting dirt and debris.
Industrial machinery is a major investment, and proper care begins with understanding the importance of lubrication. Knowing how frequently you should lubricate machines ensures they consistently perform at their peak. Every drop of attention you give to lubrication is returned tenfold in operating efficiency, reduced repair costs, and an extended lifespan for your equipment.