Safety Tips for Pneumatic Systems in Industrial Environments
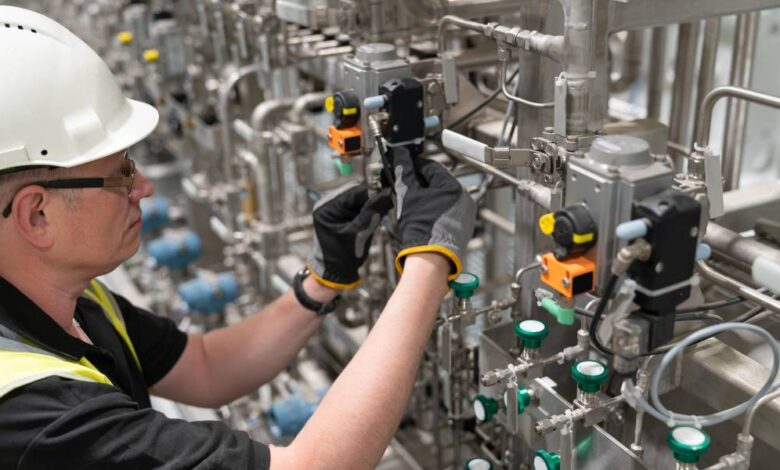
Pneumatic systems are used to power tools and machinery across various sectors of business. The high-pressure nature of pneumatics means these systems require careful handling to prevent accidents. For smoother operations that boost efficiency, following safety tips for pneumatic systems in industrial environments is vital. Ensure you’re keeping yourself and your workers up to date on the latest safety procedures to minimize risks.
1. Conduct Regular Maintenance
Maintenance is always the first step in pneumatic safety. Over time, wear and tear, along with environmental factors, can deteriorate hoses, valves, and seals. Regular checks for any signs of leaks, wear, or damage help prevent system malfunctions. Keep a maintenance schedule and use high-quality replacement components to maintain performance and reduce potential hazards.
2. Provide Proper Training
Without adequate training, even simple tasks can become safety risks. Industrial workers and technicians must understand how pneumatic systems operate and be able to identify different components and their functions. For example, knowing the different types of pneumatic valves can help workers accurately assess system configurations and optimize safety. Periodic training sessions and refresher courses ensure all team members are skilled in using the system properly and responding to any issues that arise.
3. Inspect Systems Before Use
A thorough inspection before operation can go a long way in preventing mishaps. Check the system’s connections, pressure levels, and overall stability before initiating tasks. Faulty parts or unconnected fittings can lead to dangerous outcomes under high pressure. Making sure all tools are securely attached to the system is a simple step that acts as a first line of defense against potential accidents.
4. Follow Emergency Procedures
Even with perfect maintenance and inspection routines, emergencies can occur. Familiarize yourself and your team with the system’s safety features, such as pressure relief mechanisms and emergency shutoff valves. Establish clear protocols for responding to system failures, leaks, and pressure build-ups. Minimize danger by practicing emergency drills to increase preparedness and ensure workers can respond swiftly during real incidents.
5. Avoid Overloading System Components
One of the most preventable causes of pneumatic system failures is overloading. Every system is designed with specific pressure and capacity limits. Exceeding these limits can cause pipes or fittings to burst, leading to significant risks. Ensure that the system is operating within its specified capacity and only use equipment rated appropriately for the intended pressure.
By implementing these safety tips for pneumatic systems in industrial environments, workers can protect both themselves and the equipment they rely on. These safety tips are essential practices for maintaining a secure and efficient industrial workspace.