IACMI showcases composites for automotive lightweighting in JEC Composites Pavilion at the 2019 North American International Auto Show
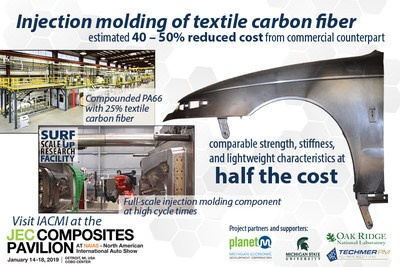
KNOXVILLE, Tenn. and DETROIT, Jan. 14, 2019 /PRNewswire/ — The Institute for Advanced Composites Manufacturing Innovation (IACMI – The Composites Institute) is showcasing composites innovations in lightweighting the automotive sector at the JEC Group’s Composites Pavilion at the 2019 North American International Auto Show (NAIAS) January 14 – 17, 2019. IACMI – The Composites Institute, a national public private partnership comprised of 160+ members, is committed to increasing domestic production capacity and manufacturing jobs across the U.S. composites industry. The institute is driven by the University of Tennessee and supported by the U.S. Department of Energy and other partners. IACMI’s participation in the Composites Pavilion is sponsored by IACMI partner, the Michigan Economic Development Corporation (MEDC).
At the Composites Pavilion, IACMI – The Composites Institute will highlight research and development initiatives that are driving the future of composites for automotive lightweighting. IACMI is showcasing the first large injection molded automotive prototype made with low-cost textile-grade carbon fiber. Produced by IACMI members Techmer PM, Oak Ridge National Laboratory (ORNL), and Michigan State University (MSU), this innovative production approach yields an estimated cost savings of 40 – 50% compared to a 50,000 filament tow commercial counterpart. The textile carbon fiber was produced by ORNL at the Carbon Fiber Technology Facility (CFTF). TechmerPM addressed unique compounding challenges to provide pellets of PA66, a commonly used thermoplastic nylon, reinforced with 25% of the textile carbon fiber. MSU tuned the molding parameters for the unique compound and produced full-size fenders through injection molding at the IACMI Scale-Up Research Facility (SURF). Through this collaborative effort, textile carbon fiber was injection molded using the Milacron 3,000-ton injection press and at cycle times relevant for high-volume production. Additional trials have demonstrated the versatility of using different fiber content, including fenders with 10% and 45% carbon fiber content.
While traditional carbon fiber composites have long been touted for their weight savings in stiffness-critical automotive applications including automotive bodies, b-pillars, and other structural components, the implementation of textile carbon fiber makes these applications more cost-competitive with traditional, heavier materials. Textile carbon fiber has potential for significant impact in the automotive industry because of the reduced cost for supporting weight savings opportunities.
“The availability of textile carbon fiber opens new opportunities for lightweighting and design innovation in the automotive industry, and we are excited to be part of the JEC Group’s Composites Pavilion to showcase this material in a molded part,” said IACMI CEO, John A. Hopkins. “We are proud of this first-of-its-kind validation of technologies and look forward to seeing future implementation in automotive and other applications.”
IACMI innovation leadership for Michigan
Much of the validation for this research project was conducted at the IACMI Scale-Up Research Facility (SURF), which is co-located with partner Manufacturing USA institute, Lightweight Innovations for Tomorrow (LIFT) in Corktown neighborhood in Detroit, Mich. SURF offers full-scale production testing of carbon fiber integration with processes from a Litzler prepreg machine to the only 4,000-ton Schuler compression molding machine available for research and development usage in North America. Additionally, the SURF also offers a 3,000-ton Milacron injection molding machine, which was utilized in this research project.
The SURF is managed and operated by IACMI partner, Michigan State University, and funded with support from MEDC, recognizing the opportunity for innovation leadership in Michigan. “The joint facility for IACMI and LIFT offers a unique opportunity to further lightweighting in the automotive industry through multi-material innovations,” said MEDC CEO, Jeff Mason. “The research done by both institutes further solidifies Michigan’s leadership in the future of the automotive industry. The innovations validated through IACMI’s textile carbon fiber project shows the attainable potential for integrating carbon fiber into the automotive industry to increase strength and stiffness in automotive components at competitive cost.”
Visit IACMI at the Composites Pavilion outside of Entrance C at the Cobo Center January 14 – 17, 2019. To learn more about the IACMI SURF, visit iacmi.org/surf.
About IACMI-The Composites Institute:
The Institute for Advanced Composites Manufacturing Innovation (IACMI), managed by the Collaborative Composite Solutions Corporation (CCS), is a partnership of industry, universities, national laboratories, and federal, state and local governments working together to benefit the nation’s energy and economic security by sharing existing resources and co-investing to accelerate innovative research and development in the advanced composites field. CCS is a not-for-profit organization established by The University of Tennessee Research Foundation. The national Manufacturing USA institute is supported by a $70 million commitment from the U.S. Department of Energy’s Advanced Manufacturing Office, and over $180 million committed from IACMI’s partners. Find out more at IACMI.org.
SOURCE IACMI – The Composites Institute