Advantages of Reaction Injection Molding
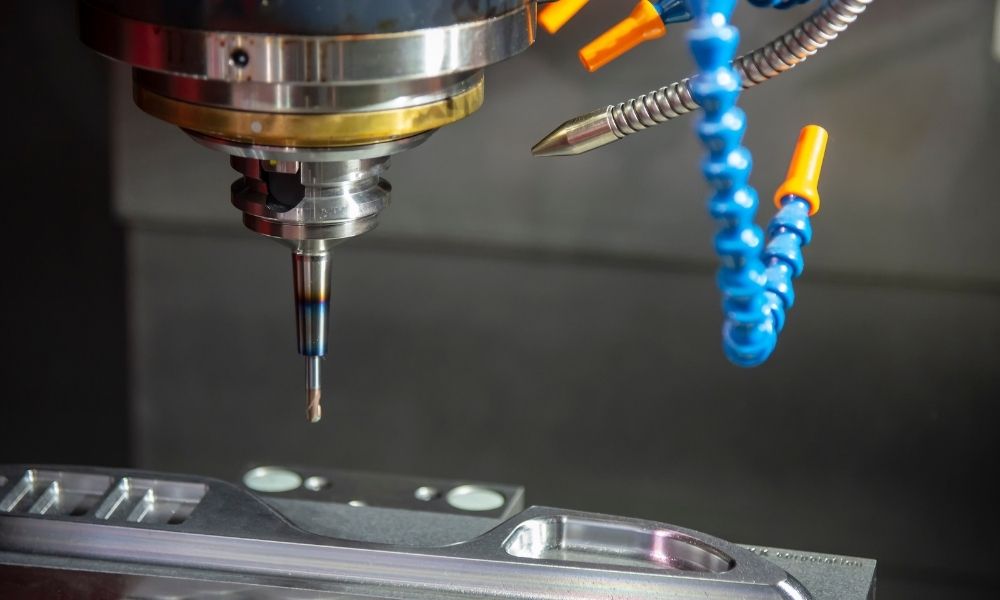
Reaction injection molding is a viable option for industrial applications where only a few large parts are necessary. The advantages of using this process range because of the chemistry and the lower temperature and pressure required compared to other molding methods. Here’s a closer look at how RIM is beneficial to various industrial applications.
Over-Molding
Because of the decreased temperature and pressure demands, RIM is the most appropriate method for over-molding, specifically for over-molding in the medical device industry. Over-molding enables production operators to combine multiple units into one with materials like steel or sheet metal.
It’s also the most appropriate option for sensitive matters like those involving valves or circuitry. These things would get destroyed in a standard high-pressure and temperature injection molding process.
Varying Thickness
Another advantage of reaction injection molding is its ability to allow for better flexibility in design. Sometimes, a different thickness is necessary. And to achieve this, you don’t want to deform or sink the part. RIM allows for varied thickness compared to standard injection processes, which must house a specified level of uniformity to prevent deforming when cooling.
Various Sizes
To produce a large part, manufacturers must often create several small parts that come together to form it. Standard injection molding typically only makes small singular units. A single RIM mold can reduce assembly expenses while having a single unit of a specified size. Additionally, an RIM mold combines many small units to create a larger unit.
Different Colors
RIM is a beneficial method from a consumer’s point of view because molds are color customizable. In comparison, a standard injection mold produces more visible design flaws and requires customization and painting at a later date.
The consumer can receive the shipped units in a specified color using RIM with the edges clear of excess material or flashing. This is a cosmetic advantage compared to other methods.
These options are best for various industrial applications, from making medical supplies to creating gaming components to testing design concepts. The benefits of using the RIM process reduce costs while increasing customization.