Previous NASA Awards for In Space Production Applications
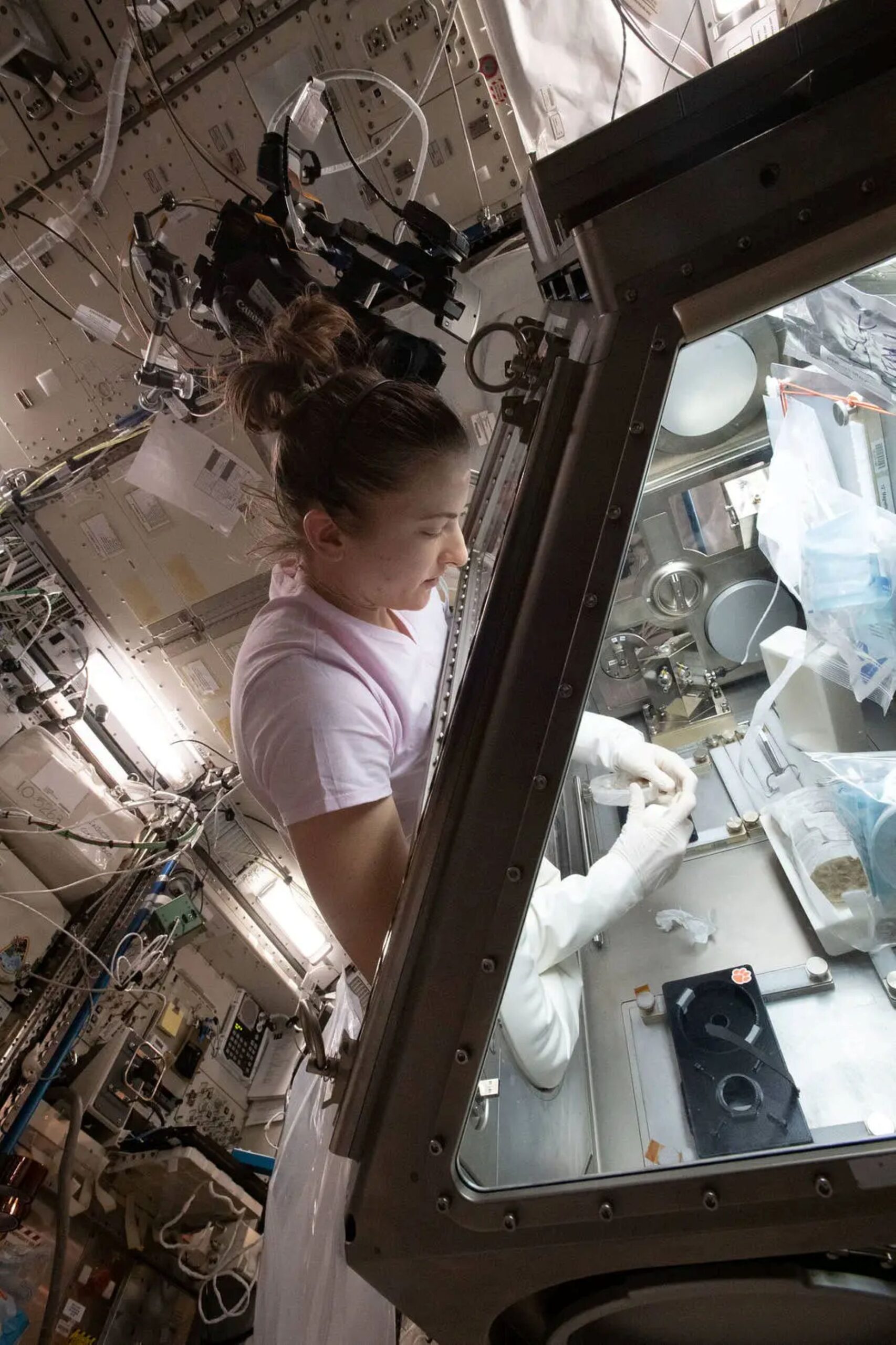
As of spring 2023, NASA has invested greater than $60M in more than twenty In Space Production Applications (InSPA) awards to U.S. entities seeking to demonstrate the production of advanced materials and products on the International Space Station. These InSPA awards help the selected companies raise the technological readiness level of their products and move them to market, propelling U.S. industry toward the development of a sustainable, scalable, and profitable non-NASA demand for services and products manufactured in the microgravity environment of low-Earth orbit for use on Earth.
- NASA Selects Proposals to Enable Manufacturing In Space for Earth (April 15, 2022)
- NASA Selects Proposals for In-Space Development of Projects Including Optical Fibers and Stem Cells and a Plan to Enable a Low-Earth Orbit Economy (April 7, 2020)
Advanced Materials
Flawless Photonics – Fabrication of Flawless Glass
Contact: Dr. Michael Vestel
Flawless Photonics of Los Altos Hills, California, in partnership with the University of Adelaide, Axiom Space, and Visioneering Space has been selected for their proposal to develop specialized glass manufacturing hardware to process Heavy-Metal Fluoride Glasses (HMFG) in microgravity. HMFG glasses are used in the terrestrial manufacturing of exotic optical fibers and other optics applications. Without convective forces present in 1g, HMFG made in microgravity are expected to achieve the ideal amorphous microstructure during synthesis, eliminating light scattering defects that limit lasing power and transmission over long fiber lengths.
Apsidal – Intelligent Glass Optics
Contact: Dr. Amrit De
Apsidal LLC. of Los Angeles, California, is developing the IGO module to process various types of complex glasses in space from which optical fibers, fiber lasers, magnetic fibers, super-continuum sources, capillary optics and adiabatic tapers can be drawn. One of the key innovations is a custom Laser Doppler Sensor for real-time in-situ analysis and feedback control of the manufacturing process. Additionally, this technology is Artificial Intelligence (AI) assisted to be adaptive and to optimize production in a low Earth orbit (LEO) environment. The microgravity environment of space is needed as gravity-induced material convection and sedimentation in complex glasses on Earth subsequently leads to unwanted crystallization, thus creating defects which reduce performance. Market areas for products from this module include specialty fibers for low-loss and high bandwidth communications, high-power fiber-amplifiers, IR counter measures, supercontinuum sources, medical applications, remote sensing, X-ray optics, and laser processing.
Fiber Optic Manufacturing in Space – Space Fibers
Contact: Dr. Dmitry Starodubov
FOMS Inc of San Diego, California, has developed a facility-class instrument for fiber fabrication in the microgravity environment to improve the quality of specialty optical fibers with the promise of up to 100x reduction in insertion loss due to the suppression of crystallization and phase separation. Two previous iterations of the facility have flown to the space station, with the third generation scheduled to launch on the 25th SpaceX cargo resupply services mission in May 2022.
Mercury Systems Torrance – Fiber Optic Production
Contact: Eric Rucker
Mercury Systems of Torrance, California, has developed a facility-class instrument for fiber fabrication in the microgravity environment to improve the quality of specialty optical fibers with the promise of up to two orders of magnitude reduction in insertion loss compared to traditional SiO2 fibers due to the suppression of crystallization and sedimentation. The first generation of the facility has flown to the space station producing over 90m of ZBLAN optical fiber from a fluorinated exotic glass preform composed of Zirconium, Barium, Lanthanum, Aluminum, and Sodium (ZrF4-BaF2-LaF3-AlF3-NaF). The second-generation FOP-2 launches on SpaceX CRS-25 in May 2022 using a nitrogen purge previously demonstrated in reduced gravity on a parabolic flight.
Redwire/Made In Space – Turbine Ceramic Manufacturing Module
Contact: Justin Kugler
Made In Space of Jacksonville, Florida, a Redwire company, is developing the TCMM to provide proof-of-principal for single-piece ceramic turbine blisk (blade + disk) manufacturing in microgravity for terrestrial use. Launched in October 2020 on Northrop Grumman’s CRS-14 mission, TCMM successfully demonstrated ceramic additive manufacturing in space for the first time in history. TCMM was also the first demonstration of stereolithography ceramic fabrication in space. The project focuses on advanced materials engineering ultimately leading to reductions in part mass, residual stress, and fatigue. Strength improvements of even 1-2 percent, as a result of being manufactured in microgravity, can yield years to decades of superior service life. Market applications include high performance turbines, nuclear plants, or internal combustion engines.
Redwire/Made In Space – Turbine Superalloy Casting Module
Made In Space of Jacksonville, Florida, a Redwire company, is developing the TSCM to provide proof of principle for polycrystal superalloy part manufacturing in microgravity for terrestrial use. Superalloys thermally processed in microgravity could have improved microstructure and mechanical properties over superalloys processed on Earth. This work expands utilization of the ISS National Lab into new commercial product areas not previously investigated.
Delivered to space station on SpaceX CRS-24 in December 2021, TSCM investigates potential improvements in superalloy microstructure by heat treating in microgravity. Market applications include turbine engines in industries such as aerospace and power generation.
Redwire/Techshot – Pharmaceutical In-space Laboratory
Contact: Rachel Ormsby
Redwire Corporation Inc. of Greenville, Indiana, has been selected for its proposal to produce small, uniform crystals as stable seed batches for pharmaceutical and institutional research customers seeking improvements/refinements in product purification, formulation and/or delivery using crystalline formulations. Their Pharmaceutical In-space Laboratory Bio-crystal Optimization Xperiment (PIL-BOX) Dynamic Microscopy Cassette (DMC) will be capable of testing multiple crystallization conditions and providing samples to be returned to Earth for analysis. When grown in microgravity, crystals are produced more uniformly and have very low size coefficients of variation thereby allowing a more stable crystal growth, high concentration, and low viscosity parenteral formulation. The proposed innovation will provide manufacturing services to companies, institutions, and agencies pursuing uniform crystallization research.
United Semiconductors – Semimetal-Semiconductor Composite Bulk Crystals
Contact: Dr. Dutta
United Semiconductors of Los Alamitos, California, has been selected for their proposal to produce semimetal-semiconductor composite bulk crystals commonly used in electromagnetic sensors for solving challenges in the energy, high performance computing and national security sectors. Together with teammates Axiom Space of Houston and Redwire of Greenville, Indiana, United Semiconductors intends to validate the scaling and efficacy of producing larger semimetal-semiconductor composite crystals under microgravity conditions with perfectly aligned and continuous semimetal wires embedded across the semiconductor matrix. If successful at eliminating defects found in those manufactured with terrestrial materials, United Semiconductors will have developed a processing technology for creating device-ready wafers from space-grown crystals.
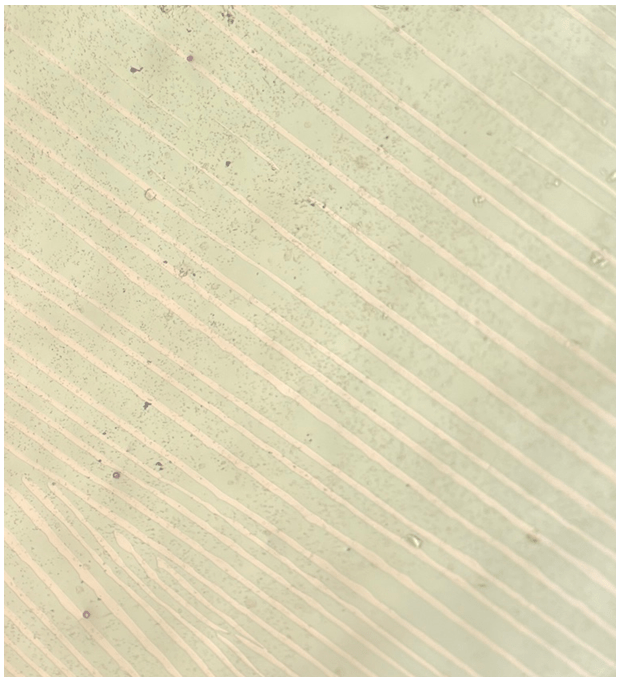
Optical Micrograph depicting the expected morphology of Semimetal-Semiconductor Composite (SSC) wafers to be extracted from space grown bulk crystals. The continuous semimetal needles embedded in semiconductor matrix will provide high yield of high-performance electromagnetic sensors. Currently this desirable morphology is seen only in a small fraction of the terrestrial grown bulk crystals. Space grown bulk crystals is anticipated to provide a significant volume of the desirable morphology.
United Semiconductors LLC
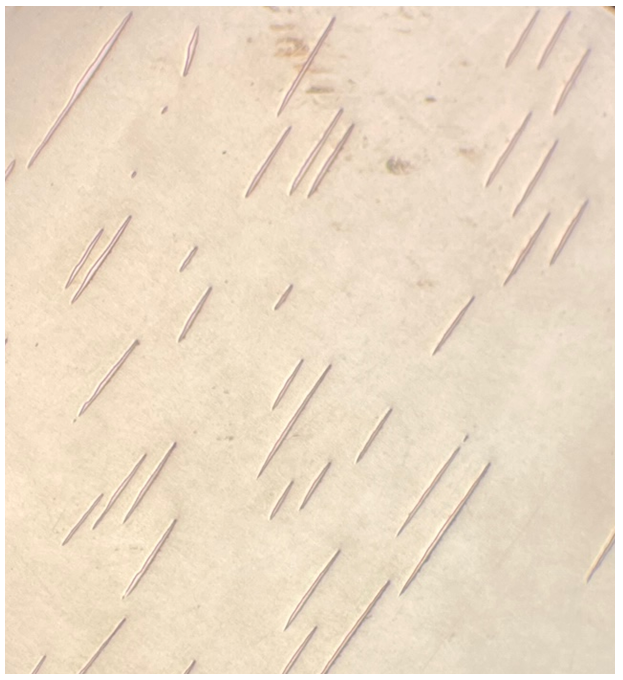
Optical Micrograph depicting the morphology of Semimetal-Semiconductor Composite (SSC) wafers extracted from terrestrial grown bulk crystals. Discontinuous semimetal needles embedded in semiconductor matrix leads to poor yield of high-performance electromagnetic sensors.
United Semiconductors LLC
Redwire/Made In Space – Industrial Crystallization Facility
Contact: Justin Kugler
Made In Space of Jacksonville, Florida, a Redwire company, is developing the ICF to provide proof-of-principle for diffusion-based crystallization methods to produce high-quality optical crystals in microgravity relevant for terrestrial use. ICF launched to the International Space Station on Northrop Grumman’s CRS-15 on February 20, 2021. It was the first facility to grow inorganic potassium dihydrogen phosphate (KDP) crystals aboard space station, offering important insight into microgravity-enabled growth processes for industrial crystals, which could yield opportunities for commercial production on-orbit. Market applications include ultra-fast optical switches, optical waveguides, optical circuit lithography, high-efficiency ultraviolet light production, and terahertz wave sensors.
Tissue Engineering & Biomanufacturing
LambdaVision/Space Tango –Retinal Implant
Contact: Alain Berinstain
Space Tango of Lexington, Kentucky, and its partner, LambdaVision of Farmington, Connecticut, are developing a system to manufacture protein-based retinal implants, or artificial retinas, in microgravity. The market for this work is the millions of patients suffering from retinal degenerative diseases, including retinitis pigmentosa (RP) and age-related macular degeneration (AMD), a leading cause of blindness for adults over 55 years old. This effort builds on a validation flight completed in late 2018 that demonstrated the proof of concept for generating multilayered protein-based thin films in space using a miniaturized layer-by-layer manufacturing device. This project will further mature the manufacturing system, producing protein-based artificial retinas in space that would be returned to Earth for preclinical evaluation of the technology. This work will establish the necessary regulatory requirements for producing biomedical products in space station, including current Good Manufacturing Practices (cGMP). The microgravity environment of space hinders convection and sedimentation in the manufacturing process, enabling more uniform layers, improved stability and higher quality thin films than can be produced on Earth. The team successfully produced 200 layers of protein on their most recent flight on SpaceX Crew-4.
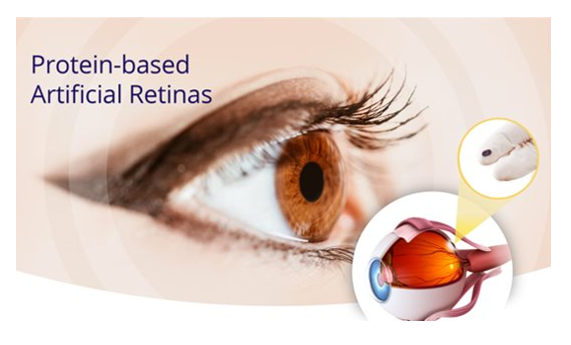
Using greater uniformity and better film deposition in microgravity to produce 100 layers of precisely aligned, precisely structured layers of bacterial rhodopsin crystals (vision protein) sandwiched between 100 layers of precisely deposited composite material with sufficient quality to enable an implantable artificial retina to FDA approval.
LambdaVision
Redwire/Made In Space – Manufacturing of Semiconductors and Thin-film Integrated Coatings (MSTIC)
Contact: Justin Kugler
Made In Space of Jacksonville, Florida, a Redwire company, is developing the MSTIC facility as an autonomous, high throughput manufacturing capability for production of high quality, lower cost semiconductor chips at a rapid rate. Terrestrial semiconductor chip production suffers from the impacts of convection and sedimentation in the manufacturing process. Fabricating in microgravity is expected to reduce the number of gravity-induced defects, resulting in more usable chips per wafer. Market applications include semiconductor supply chains for telecommunications and energy industries.
Auxilium Biotechnologies/Space Tango – Drug Delivery Medical Devices
Contact: Dr. Jacob Koffler
Auxilium Biotechnologies with Space Tango has been selected for its proposal to develop a second-generation drug-delivery medical device to more effectively treat people who have sustained traumatic peripheral nerve injury. Auxilium’s Gen 1.0 NeuroSpan Bridge is a biomimetic nerve regeneration device that guides and accelerates nerve regeneration, eliminating the need for a patient to sacrifice a nerve in the leg to repair a nerve in the arm or face. Auxilium will use its expertise in fast, high-resolution 3D-printing to adapt its proprietary platform to a Gen 2.0 3D-print device in microgravity by adding novel drug delivery nanoparticles with the potential to substantially accelerate regeneration and improve functional outcomes for people on Earth.
Lawrence Livermore National Lab/Space Tango – VAM Organ Production
Contact: Dr. Maxim Shusteff
Lawrence Livermore National Laboratory, located in Livermore, California, in partnership with Space Tango, has been selected for their proposal to adapt their terrestrial volumetric 3D bioprinting device for use in microgravity to demonstrate production of artificial cartilage tissue in space. The Volumetric Additive Manufacturing (VAM) technology is a revolutionary, ultra-rapid 3D printing method that solidifies a complete 3D structure from a photosensitive liquid resin in minutes. Because of the absence of settling and gravity-driven buoyancy and convective flows in the prepolymer, the cartilage tissues manufactured and matured in microgravity are expected to have superior structural, organizational, and mechanical properties suitable for use in long-term tissue repair and replacement.
University of Connecticut, STORRS/Axiom – Biomimetic Fabrication of Multifunctional DNA-inspired Nanomaterials
Contact: Dr. Yupeng Chen
The University of Connecticut, out of Storrs, Connecticut, in partnership with Eascra Biotech of Boston, Massachusetts and Axiom Space of Houston has been selected for their proposed biomimetic fabrication of multifunctional nanomaterials, a cutting-edge breakthrough in biomedicine that can benefit from microgravity in space to accomplish controlled self-assembly of DNA-inspired Janus base nanomaterials (JBNs). These JBNs will be used as effective, safe and stable delivery vehicles for RNA therapeutics and vaccines, as well as first-in-kind injectable scaffolds for regenerative medicine. By leveraging the benefits of microgravity, the UConn/Eascra team expects to mature in-space production of different types of JBNs with more orderly structures and higher homogeneity over what is possible using terrestrial materials, improving efficacy for mRNA therapeutics and structural integrity for cartilage tissue repair.
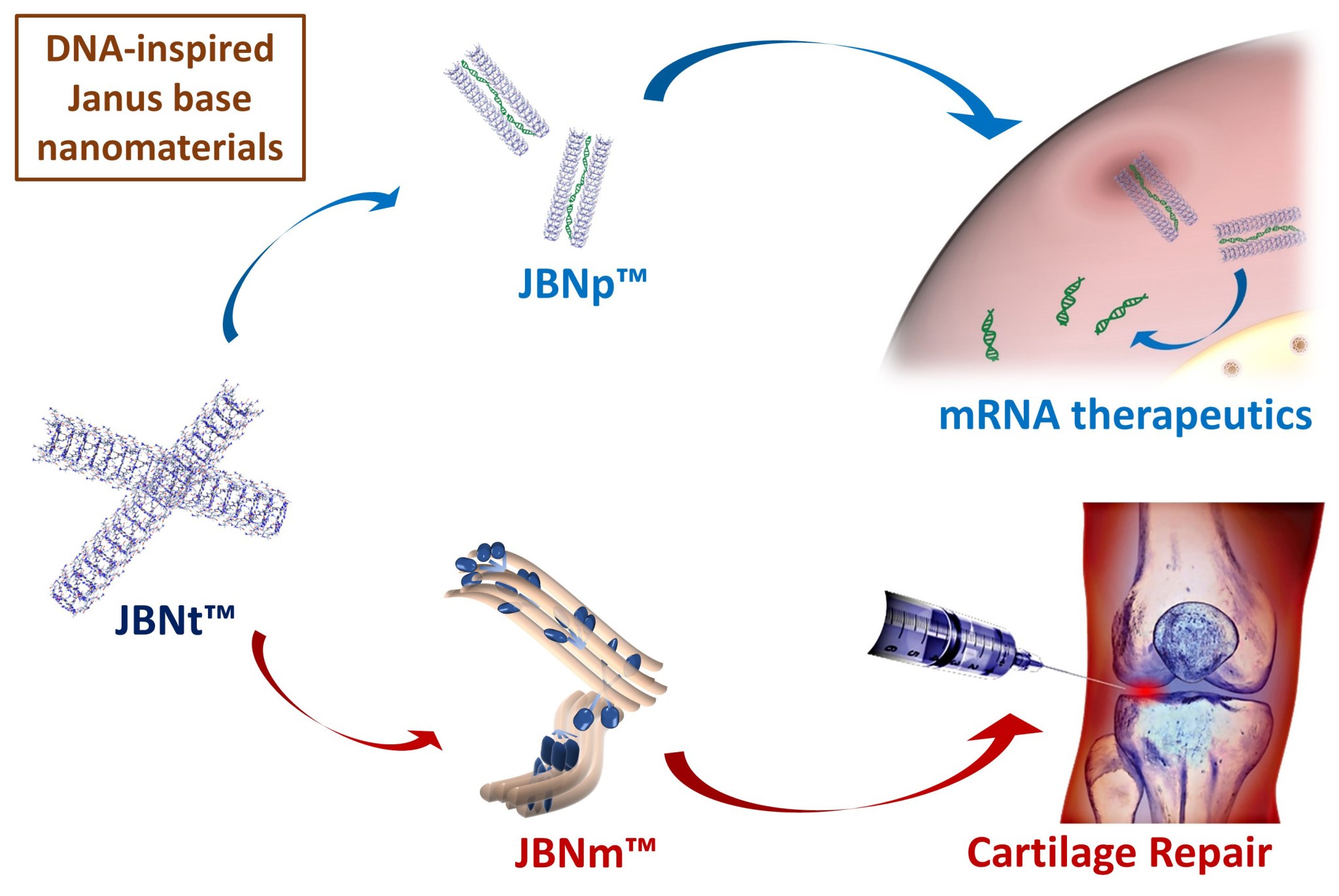
In-space manufacturing of DNA-inspired Janus base nanomaterials for delivery of mRNA therapeutics and vaccines, and tissue repair and regeneration.
Dr. Yupeng Chenu
BioServe Space Technologies with University of Colorado – Expansion of Hematopoietic Stem Cells
Contact: Dr. Louis Stodieck
BioServe Space Technologies and The University of Colorado of Boulder, Colorado, in collaboration with the Mayo Clinic, ClinImmune Cell and Gene Therapy (University of Colorado Anschutz Medical Campus), RheumaGen, and with support from Sierra Space has been selected for their proposal to develop a specialized bioreactor that will produce large populations of Hematopoietic Stem Cells (HSCs) in microgravity to treat serious medical conditions including blood cancers (leukemias, lymphomas, multiple myeloma), blood disorders, severe immune diseases, and certain autoimmune diseases, such as rheumatoid arthritis. Expansion of HSCs in microgravity is expected to result in greater stem cell expansion with less cell differentiation than is seen in 1g. If successful, the technology may enable safe and effective cell therapy transplantation, especially in children and younger adults, where long-term bone marrow cell repopulation is critical to the patient’s lifetime health.
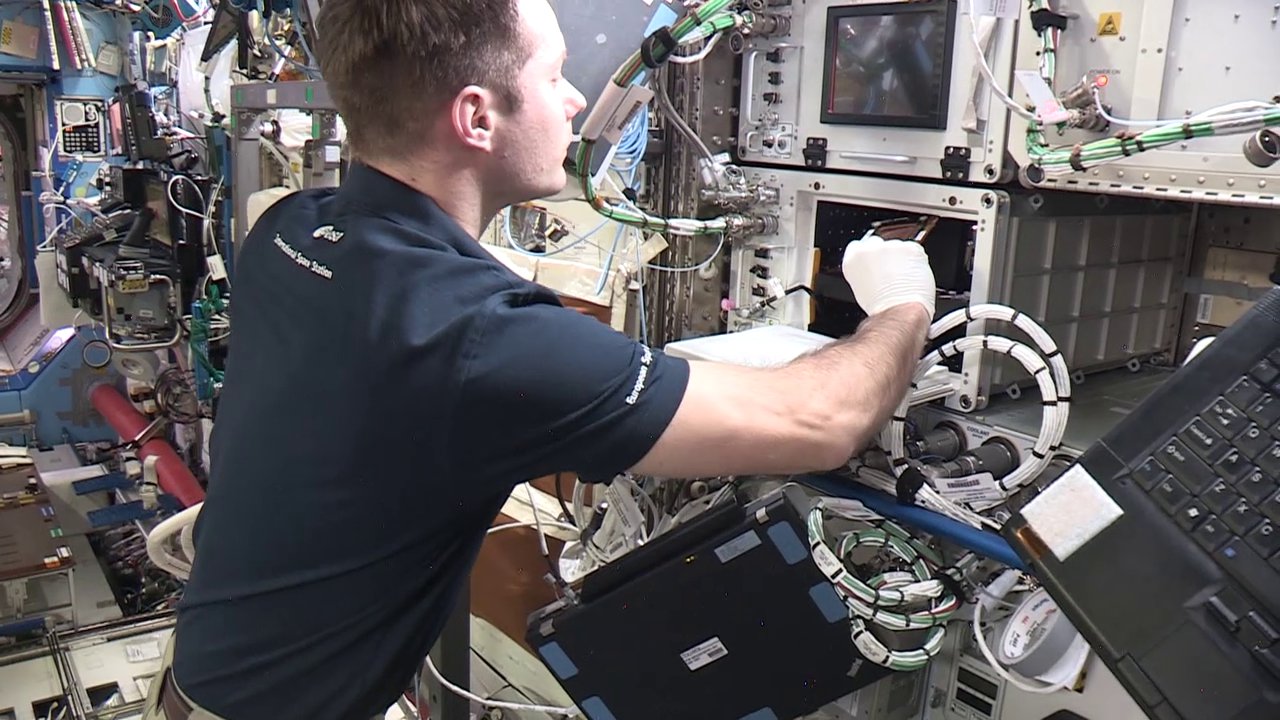
Astronaut Thomas Pesquet working in the Space Automated Bioproduct Laboratory (SABL). This image shows two SABL units, one open and one closed. SABL will be used for growing and expanding BioServe’s stem cells on board the ISS.
NASA
Cedars Sinai Regenerative Medicine Institute/Axiom – Stem Cell Therapy
Contact: Dr. Clive Svendsen
Cedars-Sinai Regenerative Medicine Institute, located in Los Angeles in partnership with Axiom Space of Houston has been selected for proposing to use cutting-edge methods related to the production and differentiation of induced pluripotent stem cells (iPSCs) on the International Space Station. Cedars-Sinai will explore in-space production of stem cells into heart, brain, and blood tissues in support of regenerative medicine uses on Earth. While stem cells and stem cell-derived tissues hold great promise for use in research and as clinical-grade therapeutic agents, safe and efficient expansion of stem cells and their derivatives continues to be a major challenge on Earth. Generating, expanding, and differentiating cells at scale in the microgravity environment of space with sufficient yields of a constant therapeutic cell product that meets FDA biologics requirements may be the answer to overcome those challenges.
Redwire/Techshot – BioFabrication Facility
Contact: Rich Boling
Techshot of Greenville, Indiana, a Redwire company, is developing the BFF as a space-based 3D biomanufacturing platform capable of printing with live human cells (autologous or allogenic). The facility contains an XYZ gantry with multiple print heads and a bioreactor cassette in the X-Y plane. Without the addition of scaffolding or chemical bio-ink thickening agents, attempts to 3D print with cells on Earth only results in creating a puddle. With scaffolding and thickening agents, organ-like shapes can be printed on Earth, but they cannot function as such. BFF prints in space with low viscosity bio-inks that only contain cells and nutrients, which enable cells to remain healthy and mobile – a necessity for creating solid thick tissue. Following a weeks-long in-space conditioning phase inside a special Redwire bioreactor, the tissue constructs are strong enough to resist gravity and remain viable following their return to Earth. In 2020, Redwire manufactured test prints of a partial human meniscus aboard the International Space Station for the company’s DoD customer, the 4-Dimensional Bioprinting, Biofabrication, and Biomanufacturing, or 4D Bio3 program, based at Uniformed Services University of the Health Sciences. The program is a collaboration between the university and The Geneva Foundation, a non-profit organization that advances military medical research. A second round of printing in space for 4D Bio3 is scheduled for late 2022 after delivery of a 2nd generation printer on SpaceX CRS-26. Redwire is planning additional bioprinting operations with the BFF, such as the Fabrication in Austere Military Environments (FAME) bioprinting program. Market applications include human tissue and organ repair or replacement.
Redwire/Techshot – Cell Reprogramming Facility
Contact: Rich Boling
Techshot of Greenville, Indiana, a Redwire company, is developing the CRF to manufacture induced pluripotent stem cells (iPSCs) in orbit using adult cells, then enabling the cells to develop into many other types of cells, that can be used inside the BFF bioprinter and on Earth for regenerative medicine, especially cell therapies. The first element of the Cell Factory system – the CRF – is in development now. Market applications include cell therapies for restorative health and autologous cell sourcing for bioprinting and vascular applications.
Cedars Sinai/Space Tango – Stem Cell Production
Contact: Alain Berinstain
Space Tango of Lexington, Kentucky, and its partner Cedars-Sinai of Los Angeles, California, are developing pilot-scale systems for the production in space of large batches of stem cells to be used in personalized medical treatment for a variety of diseases. The development of induced pluripotent stem cells (iPSC) for commercial personalized medicine applications is done in space because the work to date on the space station demonstrates stem cells retain their “stemness” for longer durations in microgravity, allowing a delay of differentiation that has the potential to enable larger batches of cells to be produced. The pilot-scale systems, built for the space station to serve as a basis for future commercial manufacturing systems, will incorporate regulatory strategies to support FDA clinical trial production of personalized medicine stem cell therapies on the space station. Including current Good Manufacturing Practices (cGMP) conditions, required for the production of stem cell therapies for human use in patients.
Sanford/Space Tango – Integrated Space Stem Cell Orbiting Lab
Contact: Alain Berinstain
Space Tango of Lexington, Kentucky, and its partners at UC San Diego/Sanford Consortium in La Jolla, California, are working to establish a new on-orbit biomedical sector for stem cell advancement, with a fully operational self-sustaining orbital laboratory anticipated by 2025. The team is working to refine current hardware capabilities and process flows, extending the capabilities of ground-based laboratories with regular access to the space station via secured flight opportunities. Stem cells differentiate into tissue specific progenitors that can be used in microgravity to better understand aging and immune dysfunction, providing an opportunity to accelerate advances in regenerative medicine and the development of potential new therapeutic approaches. The target market for this orbital laboratory is a new approach to stem cell translational medicine.
Wake Forest Institute of Regenerative Medicine/Axiom – Engineered Liver Tissue
Contact: Dr. Anthony Atala
Wake Forest Institute for Regenerative Medicine (WFIRM), located in Winston-Salem, North Carolina, has partnered with Axiom Space and BioServe Space Technologies to pursue a groundbreaking initiative. Their proposal takes advantage of the microgravity environment to develop and validate a platform that supports a ‘building block’ strategy for in-space manufacturing of vascularized and perfused liver tissue as a bridge to transplantation. This is a continuation of the NASA Centennial Vascular Tissue Challenge, where WFIRM teams won first and second place for creating metabolically active thick liver tissue that retained function for thirty days. The overarching goal is to enhance the formation of a microcapillary system within a perfusable 3D bioprinted vascularized engineered liver tissue constructs for biomanufacturing clinical-scale liver tissue constructs that allow integration into the recipient’s peripheral circulation for the treatment of liver disease. Once validated, this platform technology can produce multiple tissue construct types, including kidney and pancreas, among others. In Phase 1a, the team plans to evaluate various 3D bioprinted designs for vascularized tissue constructs to be evaluated in microgravity to identify the optimal parameters to produce liver tissue that is suitable in size to serve as a bridge to regeneration or transplantation. Phases 2 and 3 will involve biomanufacturing liver tissue constructs of the optimal design for human clinical trials and process scale-up for future commercialization.